BLDC‘s Four Major Plans (Continued)
Time:2023-05-26
Views:1037
There are four main types of overall solutions for BLDC brushless DC motors, namely MCU+pre drive+drive/MCU+[pre drive+drive]/[MCU+pre drive]+drive/SOC+drive/SOC+pre drive+drive. Through this special interview, we learned about the advantages, disadvantages, and current application status of various solutions.
Huang Zhikai, Marketing Director of the MCU Product Business Unit of Lingdong Microelectronics, analyzed these solutions. MCU+pre drive+drive is a relatively traditional method, which is also the most advantageous for general MCU companies. It is more applied in high-voltage systems or high-power systems, as high-power and high-voltage have heat dissipation and isolation issues, so most of them will adopt this method;
MCU+[pre drive+driver] can also be described as MCU+IPM. Most international manufacturers developing power components have IPM products, which provide customers with the ability to simplify the complexity of circuit board design and provide stability. It is also an early and particularly mature application method.
MCU+pre drive is one of the main development directions of smart microelectronics, which can solve the problem of limited circuit board area and greatly save customers‘ overall costs. It is currently a mainstream development direction;
The SOC method is now relatively less commonly used, mainly due to poor flexibility in SOC design. To change the driving characteristics, it is necessary to add a small MCU next to the SOC, which not only increases the cost of components but also increases the complexity of the circuit board, greatly violating the development concept of simplifying complexity.
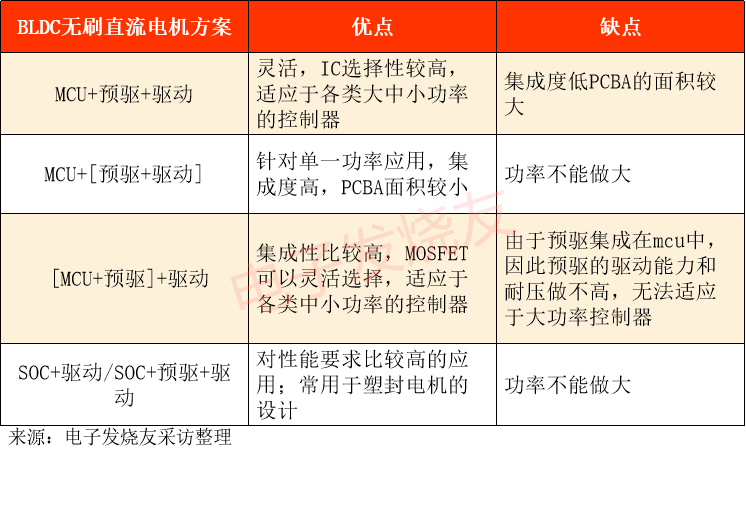
In addition to developing our own solutions, Lingdong Microelectronics also integrates solutions from our partners on the MindSPIN platform. Customers can choose SPIN products with pre drive or integrated drive, paired with a variety of solutions to design better products. This is our advantage that sets us apart from our competitors.
The solution of MPS mainly includes [ASIC+magnetic braiding]+[pre drive+drive+current sampling]/pre drive+drive solution, targeting the application market of low-voltage small and medium-sized power (0-400W) integrated motors. The MP6570 chip integrates FOC hard core control algorithm and a 14bit magnetic sensor, and is equipped with a three-phase motor drive chip that integrates pre drive and mos, or a discrete solution of three-phase pre drive and mos, making it easy to control the motor. The main advantage is the high integration of the solution, which can accelerate the customer‘s research and development process.
Renesa Electronics‘ solution belongs to MCU+pre drive, also known as BLDC motor control integrated circuit, and its product model is RAJ306000. RAJ306000 is suitable for products powered by batteries with voltages ranging from 6V to 30V, such as handheld electric tools, water pumps, micro drones, fans, etc., which are currently in its market. Compared to similar products in the market, the competitive advantage of RAJ306000 lies in its ability to not only support 120 degree conduction control without Hall sensors, but also support low speed and high torque starting.
Pinjia provides corresponding technical support for various solutions based on RT series MCU and Infineon pre drive and driver products. If Infineon uses a solution of MCU+pre drive+driver, Pinjia can provide corresponding technical support based on RT7100+RT7024+Infineon MOSFET solution. Infineon MCU has a main frequency of up to 144 MIPS, built-in MAC and FPU units, effectively reducing complex computing time; In addition, Infineon offers various specifications of pre drive series products and various specifications of drive products such as Mosfet, IGBT, IPM, etc. for selection.
In addition, Pinjia‘s Microchip motor solution is MCU+pre drive+drive. Microchip dsPIC MCU with a main frequency of up to 100MIPS and built-in DSP? The engine greatly reduces complex computing time and integrates on-chip operational amplifiers, making the overall solution more concise.
Cypress provides motor control solutions based on PSoC (MCU). Its differentiated competitive advantage is reflected in the high integration of PSoC (MCU), providing different motor control solutions and customized technical support, such as mature and reliable, industry-leading motor control technology and algorithms, tailorable motor control libraries based on different applications, achieving customer mass production solutions, and using different drivers based on customer choices (separate IGBT/MOSFET or integrated IPM), Training and support in motor control technology.
Scheme for Switched Reluctance Motors
In this interview with electronics enthusiasts, most of the surveyed manufacturers did not offer a solution for switched reluctance motors, only Cypress provided a solution for switched reluctance motors, while Lingdong Microelectronics is in the laboratory stage. MPS and Renesa Electronics have stated that they do not have any relevant solutions.
The main motivation for the development of switched reluctance motors comes from the use of rare earth elements in brushless DC motors, as the development of rare earth elements has pollution issues and belongs to regulated materials, resulting in the development of switched reluctance motors. Huang Zhikai said that China has nearly 90% of the production of rare earths, and not all brushless DC motors must use rare earth materials. Therefore, developing reluctance motors in China may not necessarily have advantages. In addition, the drive of switched reluctance motors is prone to noise and poor efficiency, so it has not yet been widely used in visible products on the market.
According to Nelson Liu, the application engineering manager of Pinjia Group, the switched reluctance motor is also a new technology in electric motors. The salient poles of its stator and rotor are laminated with ordinary silicon steel sheets, and the rotor has neither winding nor permanent magnet. The stator poles are wound with concentrated windings, and the two radially opposite windings are connected, resulting in a simpler structure. When the number of phases increases, its structure is complex, and there are many main switching devices with high costs. Nowadays, four phase (8/6) structures and three-phase (12/8) structures are widely used. Due to its structural characteristics, it is only suitable for machinery that requires heavy load starting and long-term low-speed heavy load operation due to its drawbacks such as high noise and vibration. In addition, there are relatively few engineers specializing in reluctance motors and controllers.
Seplasky‘s switched reluctance motor control scheme for FM3 has been mass-produced by customers. Peng Tao, the Asia Pacific market manager of the Cyberspace IoT wireless business unit, stated that in 2019, Cyberspace will provide more cost-effective control solutions based on PSoC4 chips. Switched reluctance motors can optimize motor costs due to their smaller size, but their current maturity limits their development.
How to choose BLDC with multiple manufacturers and solutions?
Open platforms and products. Huang Zhikai‘s suggestion from Lingdong Microelectronics is that a good chip company with a brushless motor solution must maintain an open mindset to provide customers with better products and choices, and must not start from tying customers down and leaving them with no space in the future. MM32SPIN series MCU and MindSPIN developed by Lingdong Microelectronics? The platform is very open, and customers can freely switch and select models in the MM32SPIN series MCU. MindSPIN? The platform‘s solution can also be widely applied to different MM32SPIN models, and most of the provided driver examples are open, allowing everyone to learn and learn from each other. Customers must consider future upgrade compatibility when choosing, and should not be greedy for the convenience of using the unique IC of a single product. Not only will developing more diversified products in the future be unable to meet the needs of customers, but it is more likely that the original factory will tie the customer‘s mentality of being unable to replace and cause derivative problems such as shortage and price increase. Therefore, choosing a chip company with the foresight to develop new products and maintain an open mindset is our suggestion.
Evaluate in terms of price and development cycle. Pinjia Nelson recommends that most customers evaluate two aspects when choosing a solution. One is the price. In cases where the technical advantage is not very obvious, customers will prioritize choosing solutions with price advantages. The second is the development cycle. If the development cycle of the product has obvious advantages, customers will also prioritize it. The Richek solution supports UL60730 certification, which can save more than 3 months of development cycle on exported products, greatly saving product development costs. Diversification of products is also a good choice for customers. Richek offers support for single driver, two in one, and three in one solutions.
Fashion is not as good as what suits oneself. Peter Shen, senior manager of Pinjia Group, believes that selecting appropriate solutions based on application needs is currently the most popular method, which is sine wave control. However, in situations where application requirements are not high, square wave control can be chosen. In addition, according to the application scenario of the motor, the method of inductive control can also be selected, which makes the program processing simpler and does not necessarily require non-inductive control.
Wang Li, a senior FAE from MPS North China, also believes that the main focus is on selecting suitable solutions based on the characteristics of the application. For example, if the design input is not yet very certain and there may be significant adjustments in the future, the MCU+pre driver+Mos solution is undoubtedly the preferred solution. If the input is relatively certain and the design pursues miniaturization, integration, and speed, then the MP6570 (FOC hard core+magnetic encoding) similar to MPS is a good solution.
Reliable stability and technical support. For customers choosing motor control solutions, Cypress Pengtao suggests that they should consider several factors: 1. the reliability and cost-effectiveness of the chip, 2. the stability and maturity of the control solution, and 3. technical support for the control solution. Cypress‘s PSoCMCU integrates high-speed analog-to-digital conversion, operational amplifiers, and comparators to optimize BOM costs. The widespread application in the market, especially in the home motor control market, has proven the maturity and reliability of chips and solutions. Especially the Cypress motor control application team, which has been focusing on motor control for more than ten years, continuously develops and leads motor control algorithms and technologies, and can provide excellent technical support for customers.
In addition, matching motors from different manufacturers requires additional debugging, which manufacturers have fully considered. The MP6570 based solution provided by MPS is a built-in FOC hardcore solution, which only needs to complete system configuration through corresponding register settings. At the same time, it provides a friendly GUI, allowing users to complete debugging more conveniently.
Ruisa Electronics‘ RAJ306000 solution has undergone extensive debugging based on the commonly used BLDC motors for handheld electric tools. Currently, the Firmware provided can adapt to many BLDC motors in the market. Even if the specifications of customers‘ BLDC motors are special, Ruisa Electronics‘ engineers can help customers debug different versions of Firmware to meet their different requirements.
Infineon adopts exclusive solutions and optimized adaptive algorithms for different industries to solve the problem of motor matching.
The Microchip motor solution has predefined motor specific parameters in the software. For non motors, it is only necessary to understand their individual parameters and modify them appropriately in the software.
Richtek‘s latest differential design solution effectively solves the problem of motor load adaptation. With the development of human-machine interface debugging of motor parameters, it can greatly reduce the workload of engineers.
At present, Lingdong Microelectronics provides debugging instructions and regular training sessions, and also collaborates with many solution providers with engineering capabilities to solve problems that require a large amount of engineering manpower. In the future, we will also provide more diverse interfaces such as automation and adaptation, making design easier.
In Cypress‘s motor control scheme, a user file is provided in the software, which mainly records the magnetic and electrical parameters of the motor used by the user. By configuring this file, Cypress‘s motor control software can automatically adjust motor control without the need for a large number of engineers to debug. Moreover, in the software algorithm of Cypress, the tolerance rate for motor parameters is relatively high, and good motor control can be achieved within a parameter error range of 15-20%.
Disclaimer: This article is transferred from other platforms and does not represent the views and positions of this site. If there is any infringement or objection, please contact us to delete it. thank you! |