Three New Design Sites for Improving Motor Drive
Time:2023-05-25
Views:1015
The technological advancements in motor driven design have opened many doors. For example, in motion control systems, higher accuracy, efficiency, and control provide many benefits in terms of user experience and safety, resource optimization, and environmental friendliness. The introduction of brushless motor technology is an important step in improving overall efficiency.
The transition from brushing to brushless began some time ago and continues to develop with the introduction of more new technologies and system components. However, at the same time, new developments in electronic components can achieve better thermal management, higher power density, and miniaturization, while allowing for more complex tasks to be performed at competitive costs.
Using first-class semiconductor technology, low-voltage and medium voltage motor designs can be more efficient, smaller, and provide more powerful functionality for end users. Here, engineers can choose different semiconductor solutions to fine-tune their motor drive design.
The technical parameters such as switching frequency and thermal resistance of the terminal product set the requirements for the driver. Next, in order to build an optimization system that can better improve power density and reduce size, designers must minimize losses (including conduction losses and switching losses) and optimize thermal management.
This article focuses on three design scenarios for creating more compact, efficient, and high-performance motor drives.
Improvement of Power Packaging Technology
With the increasing trend of battery voltage in robots and electric tools, the power driven by motors is also increasing. This means that the requirements for high rated current, durability, and extended service life of power semiconductors are becoming increasingly high. An important place to address these requirements is the new packaging technology platform, which provides three different variants based on specific requirements (Figure 1).
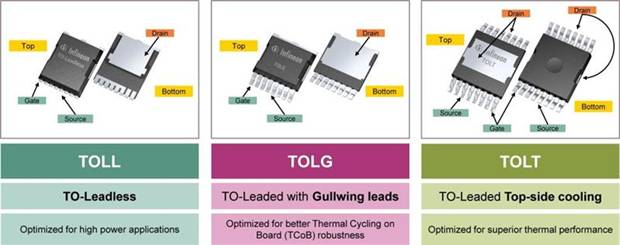
Figure 1 shows a broad comparison of TOLL, TOLG, and TOLT packaging technologies. Data: Infineon
TO-leadless (TOLL) has been optimized to handle currents up to 300 A, while increasing power density and significantly reducing floor space. Compared to D 2 PAK, it reduces floor area by 30%, height by 50%, and overall space by 60%, resulting in a more compact design.
The TO lead gull wing (TOLG) package provides a package that is compatible with the TO lead-free package. Compared to TO without leads, the additional function of gull wing leads can increase the performance of on board thermal cycling (TCoB) by two times. This package exhibits excellent performance on an aluminum insulated metal substrate (Al IMS) board.
TOLT is the top cooling package for the O lead in the TOLx series. By cooling at the top, the drain is exposed to the packaging surface, allowing 95% of the heat to be directly dissipated to the heat sink. Compared with TOLL packaging, R thJA is increased by 20% and R thJC is increased by 50%.
Three phase gate drive controller IC
The new three-phase intelligent motor driver IC supports the development of high-performance motor drivers using brushless direct current (BLDC) or permanent magnet synchronous (PMS) motors. These designs are particularly suitable for mobile robots, drones, and electric tool applications.
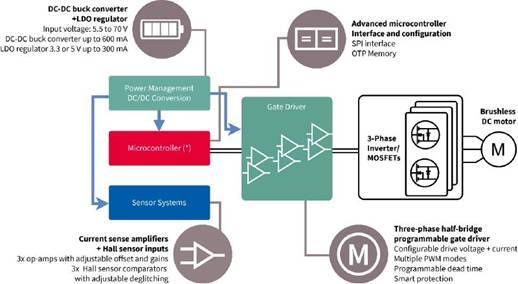
The gate driver controller IC in Figure 2 can be integrated with the microcontroller in one package. Data: Infineon
By using over 50 programmable parameters with built-in digital SPI interfaces, the motor driver IC has high configurability and can drive a wide range of MOSFETs, resulting in system efficiency. Other benefits include:
Reduce external components and PCB area
• Optimize efficiency and electromagnetic interference (EMI)
Flexibility of using different inverter FETs
High precision current sensing while saving external components
• Higher dynamic range to improve signal resolution
• Improve reliability and fault detection
• GaN for improving efficiency and power density
In some cases, an important design goal is to integrate power electronic devices near the motor or within the same enclosure. Potential benefits include higher power density, lower bill of materials (BoM) costs (because motors and electronics can be placed in smaller enclosures), and cost savings due to higher system efficiency.
Usually, heat dissipation and large capacitance have been limiting factors for integrated motor drives (IMDs). The shift towards gallium nitride (GaN) based design lays the foundation for overcoming the challenging trade-off between switching speed and output power. The higher switching frequency that can be achieved through the use of field-oriented control (FOC) can bring numerous system advantages, including reducing large capacity capacitors, reducing motor ripple current, reducing torque ripple, and reducing noise. Higher frequencies can also lower the motor temperature. This combination leads to higher end-to-end system efficiency improvements.
In drones, the system efficiency advantage not only makes the design more efficient because of lower losses but also smaller volume, which is a key advantage in making drones lighter and have longer flight times.
Moving towards the future
Higher product integration makes it easier for engineers to implement ready-made solutions, thereby reducing time to market. Combining high integration with a wide range of programmable features, such as in motor driver ICs, can bring competitive advantages and system flexibility. Next, the new packaging and broadband gap technology provide additional advantages for motion control systems, such as:
The new packaging design provides optimized thermal management, as switch losses are always accompanied by heat in the power switch.
The new broadband gap device lays the foundation for driving higher switching frequencies, helping to improve accuracy and size.
To develop competitive motion control systems, designers must utilize all available technologies.
Disclaimer: This article is transferred from other platforms and does not represent the views and positions of this site. If there is any infringement or objection, please contact us to delete it. thank you! |