Discussion on SMT chip dispensing process and technical requirements
Time:2023-07-22
Views:830
The combination of through-hole insertion (THT) and surface mount (SMT) for lead components is the most commonly used assembly method in current electronic product production. In the entire production process, one component of a printed circuit board (PCB) can only be soldered by wave soldering after being glued and solidified at the beginning, which takes a long time. Additionally, there are many other processes involved, making the solidification of the component particularly important. Therefore, the research and analysis of the glueing process is of great significance.
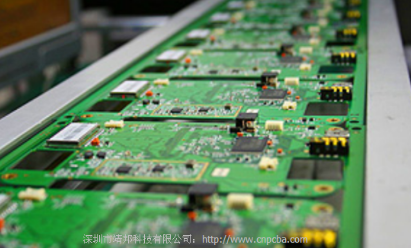
1、 SMT chip processing adhesive and its technical requirements:
The glue used in SMT is mainly used for the wave soldering process of surface mounted devices such as chip components, SOTs, and SOICs. The purpose of using glue to fix surface mounted components on the PCB is to avoid the possibility of component detachment or displacement under the impact of high temperature waves. In general, epoxy resin heat curing adhesive is used in production, rather than acrylic acid adhesive (which requires UV radiation curing).
2、 Requirements for SMT work on patch adhesive:
2.1. Glue should have excellent thixotropic properties;
2.2. No wire drawing;
2.3. High wet strength;
2.4. No bubbles;
2.5. The curing temperature of the adhesive is low and the curing time is short;
2.6. Have sufficient curing strength;
2.7. Low moisture absorption;
2.8. Have good repair characteristics;
2.9. Non toxicity;
2.10. The color is easy to identify, making it easy to check the quality of the adhesive points;
2.11. Packaging. The packaging type should be convenient for the use of the equipment.
3、 Process control plays a crucial role in the dispensing process.
The following process defects are prone to occur in production: substandard adhesive spot size, wire drawing, adhesive immersion welding pad, poor curing strength, and easy peeling. To solve these problems, it is necessary to study various technical process parameters as a whole in order to find a solution to the problem.
3.1. Size of dispensing amount
Based on work experience, the size of the adhesive spot diameter should be half of the pad spacing, and the adhesive spot diameter after patch placement should be 1.5 times the adhesive spot diameter. This ensures that there is sufficient glue to bond the components while avoiding excessive glue contamination of the solder pads. The amount of glue dispensed is determined by the rotation time of the screw pump. In practice, the rotation time of the pump should be selected based on production conditions (room temperature, adhesive viscosity, etc.).
3.2. Glue dispensing pressure (back pressure)
The current dispensing machine uses a screw pump to supply the dispensing needle, and the hose adopts a pressure to ensure sufficient glue supply to the screw pump. Excessive back pressure can easily cause glue overflow and excessive glue volume; If the pressure is too low, intermittent dispensing and leakage may occur, resulting in defects. The pressure should be selected based on the same quality of adhesive and working environment temperature. A high ambient temperature will reduce the viscosity and improve the fluidity of the adhesive. At this point, it is necessary to lower the back pressure to ensure the supply of adhesive, and vice versa.
3.3. Needle size
In practical work, the inner diameter of the needle should be 1/2 of the diameter of the dispensing point. During the dispensing process, the dispensing needle should be selected based on the size of the solder pad on the PCB: for example, the solder pad sizes of 0805 and 1206 are not significantly different, and the same type of needle can be selected. However, for pads with significant differences, different needles should be selected to ensure the quality of the dispensing point and improve production efficiency.
3.4. Distance between needle and PCB board
Different dispensing machines use different needles, some of which have a certain degree of stopping (such as CAM/A LOT 5000). At the beginning of each work, the distance between the needle and the PCB should be calibrated, that is, the Z-axis height should be calibrated.
3.5. Glue temperature
Generally, epoxy resin adhesive should be stored in a refrigerator at 0-50C, and should be taken out 1/2 hour in advance before use to ensure that the adhesive is fully compatible with the working temperature. The usage temperature of glue should be 230C-250C; The ambient temperature has a significant impact on the viscosity of the adhesive. If the temperature is too low, the adhesive point will decrease and wire drawing phenomenon will occur. A difference of 50C in ambient temperature can cause a 50% change in the amount of glue applied. Therefore, the ambient temperature should be controlled. At the same time, the temperature of the environment should also be guaranteed, as small humidity can easily dry the adhesive points and affect the bonding strength.
3.6. Viscosity of glue
The viscosity of the adhesive directly affects the quality of dispensing. If the viscosity is high, the adhesive point will decrease, and even wire drawing will occur; When the viscosity is low, the adhesive point will increase, which may contaminate the solder pad. During the dispensing process, choose a reasonable back pressure and dispensing speed for adhesives with different viscosities.
3.7. Curing temperature curve
For the curing of adhesive, the general manufacturer has provided a temperature curve. In practice, higher temperatures should be used for curing as much as possible to ensure sufficient strength of the adhesive after curing.
3.8. Bubbles
The glue must not have bubbles. A small gas can cause many solder pads to lack glue; Every time the rubber hose is replaced midway, the air at the connection should be drained to prevent the occurrence of empty tapping.
For the adjustment of the above parameters, it should be done from point to surface. Any change in one parameter will affect other aspects, and the occurrence of defects may be caused by multiple factors. Possible factors should be checked one by one to eliminate them. In short, in production, various parameters should be adjusted according to the actual situation, to ensure production quality and improve production efficiency.
Disclaimer: This article is transferred from other platforms and does not represent the views and positions of this site. If there is any infringement or objection, please contact us to delete it. thank you! |