Xuanzhi Technology Ding Wen, Xu Shuo, Application Details of 12V DC Brushless and Brushed Motor Control Chips for Vehicles
Time:2024-01-03
Views:173
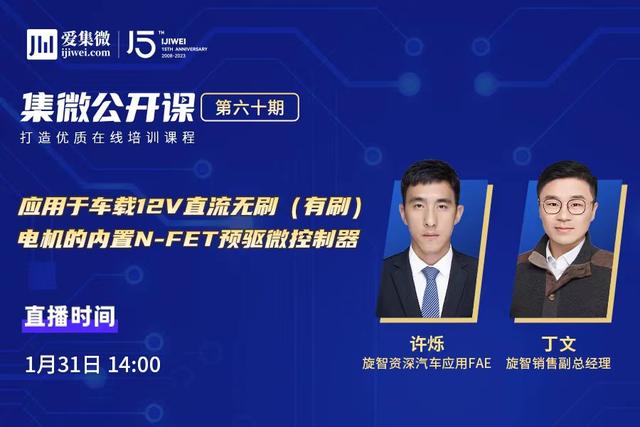
This type of usage scenario, which is usually powered by a low-voltage 12V network, often has extremely high requirements for scheme BOM cost, weight and volume, conversion efficiency, etc. Therefore, the mainstream solution for motor control has gradually formed the integration of MCU, pre drive, power management LDO, and bus transceiver into a single chip.
It is obvious that motor control chips have broad prospects and are expected to achieve maximum market value and scale application in the automotive industry, but they have often been at the top of the chip shortage list in the past two years.
On the afternoon of January 31st at 14:00, Jiwei Network held the 60th "Jiwei Open Class" activity, inviting Ding Wen, the Deputy General Manager of Sales of Xuanzhi Electronic Technology (Shanghai) Co., Ltd. (referred to as Xuanzhi Technology), and Xu Shuo, a senior automotive application FAE, to share an online live broadcast with everyone on the theme of "Built in N-FET Pre drive Microcontroller for 12V Direct Current Brushless (Brushed) Motors in Vehicles", to explain the technical knowledge of the product The core functional characteristics of the solution and the research and development of Xuanzhi Technology.
Originating from the semiconductor industry, West Point Military Academy
Mr. Ding Wen first briefly introduced the development history of Xuanzhi Technology to the audience. The company was formerly known as the Motor Industry Line Division of Xiantong Semiconductor Company, which was spun off and operated independently through MBO at the end of 2014. Currently, it has branches in Shanghai, Shenzhen, Qingdao, Hong Kong and other places. The company focuses on the research and development of high integration motor control chips and advanced core algorithms, Most members of the founding core team have years of experience in research and development, marketing, and management in world-class semiconductor companies.
Since independence, Xuanzhi Technology has successfully mass-produced two generations of motor control chips and applied them in large quantities in the fields of white electronics and industrial control. With the product differentiation ability brought by the chip IP and algorithm core technology advantages, it has successively entered the supply chain of domestic and foreign leading customers such as DJI, Ninth Segway, Gree, Midea, Haier, Bosch, EBM, etc. The cumulative shipment volume of major customers has reached nearly 60 million.
In recent years, Xuanzhi Technology has also actively laid out automotive grade products. Its highly integrated automotive grade motor control SoC products have undergone years of development, testing, and polishing, and have officially entered the mass production and sample delivery stage by the end of 2022. Ding Wen revealed that Xuanzhi Technology has a thorough understanding and rich experience in automotive electronic function safety and quality reliability, and is about to obtain ISO26262 ASIL-D system management certification.
Ding Wen stated that the 12V DC motor for automobiles can be mainly divided into application scenarios such as thermal management, vehicle body, chassis, etc., and the driving schemes are also different. For multi motor control scenarios such as rearview mirrors and seat adjustments, the driving scheme is usually MCU paired with multiple half bridge drives, while for single motor scenarios, further power division is required. For low-power scenarios such as air doors, water valves, and seat ventilation, all in one single chip solutions can be used. Overseas brands such as Melexis and TDK are currently more common, but as the power gradually increases, in medium power scenarios such as water pumps, oil pumps, and blowers, all in one single chip solutions can be used Cooling fans, wipers, car windows, sliding doors, and LiDAR often use SoC combined with MOS tubes. In high-power single motor scenarios, such as EPS and brakes, a discrete scheme is generally adopted, which requires good functional safety level of the chip and redundancy in system design.
Targeting the rapidly growing medium power single motor control scenario, the SPD1179 from Xuanzhi Technology provides a highly competitive domestic solution for vehicle specifications.
SPD1179 New Features
Xu Shuo, a senior automotive application expert at Xuanzhi Technology, further explained the technical characteristics and reference design of SPD1179 to the audience.
According to Xu Shuo‘s introduction, the main application scenarios of SPD1179 include three-phase brushless DC motors for fans and pumps, as well as H-bridge control for brushless DC motors for windows, skylights, and wipers. It is already in the mass production and sample delivery stage and is planned to be mass-produced in the third quarter of this year and obtain SIL-B/AEC-Q100 dual certification. It can be used to replace mainstream products such as Infineon TLE989x/8x/7x/6x/5x, NXP S912ZVMB/L/C, and Mailaixin MLX81340/4/6.
Xu Shuo stated that SPD1179 is sealed by MCU and high-voltage module, with packaging specifications of QFN48/QFN56. It uses a 32-bit Cortex-M4 core equipped with floating-point operation unit, with a maximum main frequency of 100MHz. The chip provides a maximum storage space of 128K Flash+32K RAM, comes with 1KB EEPROM, and can operate in a voltage range of 5.5V-40V. It also supports LIN, CAN/CANFD vehicle specific standard protocols.
SPD1179 also has built-in single ended operational amplifiers and differential operational amplifiers. The single ended operational amplifier can be used for bus current sampling, while the differential operational amplifier is used for phase current sampling and reconstruction. It has a complete hardware protection mechanism to ensure fast protection during motor driving. The ECAP (Enhanced Pulse Capture Module) has a Dual pin mode, which can simultaneously calculate the frequency and duty cycle of different input pin signals. The timer has multiple modes such as gate, The enable count of the timer can be controlled through external GPIO levels or edge signals. The product also supports downloading and burning programs through UART or LIN interfaces in ISP mode. The high-voltage module is based on current type driving, with programmable configuration driving capability. MOS control is more flexible, using VCP-based architecture, eliminating bootstrap capacitors and saving design costs. The high-voltage MON pin can capture high-voltage PWM signals through ECAP, The product meets both ASIL-B and AECQ100 certifications for functional safety.
After summarizing the overall system diagram, Xu Shuo introduced the characteristics of functional modules such as SPD1179 power management, analog-to-digital conversion ADC, programmable gain amplifier (PGA), analog comparator, phase comparator, PWM, pre drive, VDS protection, etc.
In the power management module, SPD1179 uses a single power supply ranging from 5.5 volts to 40 volts, with internal integration of 5 volts, 3.3 volts, and 1.2 volts LDO. It has current driving capabilities of 80 milliamps, 50 milliamps, and 40 milliamps respectively, supports three power modes (active, stop, and sleep), and has power domain detection and overcurrent, overvoltage, and undervoltage protection mechanisms. The overall power on time of the system is less than 5ms, and the chip can be awakened through various methods such as LIN, MON, cyclic wakeup, and GPIOs.
Based on functional safety requirements, 1179 also has a built-in power monitoring module, which buffers critical power signals to a 13 bit Monitoring ADC through a power tracking amplifier to monitor power status.
SPD1179 Reference Design
As is well known, new products from chip manufacturers often require reference design solutions to lower the development threshold for downstream users, accelerate market launch. At the end of the open class, Xu Shuo also introduced the reference design and supporting software and hardware development toolchain based on SPD1179 to the audience.
Xu Shuo stated that in addition to the minimum system, the Demo board provided by Xuanzhi Technology also includes power supply high side anti reverse connection and filtering circuits, three-phase inverter bridge circuits, single resistance sampling and filtering circuits, bus current sampling circuits, external PWM signal input detection circuits, LIN and CAN communication circuits, etc.
In the three-phase inverter bridge circuit, the current type pre drive architecture of SPD1179 can omit the driving resistor Rg and external bootstrap capacitor CBOOT. When driving MOS, it can be directly powered by VCP, and its current driving ability can be flexibly modified through registers.
In the single resistor sampling and filtering circuit, the current signal flowing through the sampling resistor can be directly input to the DPGA input pin at the chip end through a simple RC filtering circuit. After internal amplification, AD sampling is used in conjunction with relevant algorithms to complete three-phase current reconstruction.
In the application scenario where PWM duty cycle is used as a control command in the external PWM signal input detection circuit, the signal can be transmitted to the chip ECAP module through the PWM input detection circuit to calculate the corresponding frequency and duty cycle.
The bus current sampling circuit can input the sampled resistance signal into the chip for single ended amplification and sampling after bias calculation and filtering with a large RC constant.
In terms of LIN and CAN communication circuit, SPD1179 has a built-in CAN Controller, which can achieve CAN/CANFD communication in conjunction with the onboard TJA1043/1044 CAN Transceiver standard reference circuit. The onboard LIN communication reference circuit has LIN communication capability.
Regarding the development toolchain, Xu Shuo introduced that Xuanzhi Technology can provide algorithm Flm files specifically for code burning, and also support IAR and KEIL development. Debugging can be done through this JScope to observe internal variables, and data can be uploaded to Matlab for analysis through high-speed interfaces. Matlab‘s Simulink can also be used for motor control algorithm design.
Disclaimer: This article is transferred from other platforms and does not represent the views and positions of this site. If there is any infringement or objection, please contact us to delete it. thank you! |