Using GaN for automotive voltage reduction and reverse boost converters, efficient 48V distribution can be achieved
Time:2024-03-13
Views:247
The increasing trend of electrification in the automotive industry enables car manufacturers to provide new innovations to the market at a cost-effective cost while also meeting increasingly stringent emission legislation. Raising the main bus voltage of the vehicle to 48V helps meet the needs of power consuming systems, such as the start stop motor/generator of mild hybrid vehicles, as well as loads such as electric power steering, electric boosting, vacuum pump, and water pump.
Compared to the traditional 12V automotive power standard, 48V distribution can provide four times more power without increasing cable thickness, weight, and cost. By 2025, it is expected that one in every 10 cars will be a 48V mild hybrid vehicle.
However, giving up the established 12 volt power system immediately is not an economic choice. In practice, 48V and 12V infrastructure will coexist in future generations of vehicles. In order to ensure satisfactory operation of this dual voltage setting, each one is aimed at ensuring phase current balance, and the use of precision shunt resistors for current detection is superior to inductor DCR current detection. However, shunt resistors with a rated current exceeding 70 A typically occupy a larger space, resulting in higher parasitic inductance, leading to high noise and saturation of the current detection amplifier, resulting in ineffective measurements. A simple solution to overcome this problem is to add an RC filter network with a matching time constant to eliminate parallel inductance. This design uses a current detection amplifier with a bandwidth of 500 kHz and a 50 V/V gain, which can generate a total current detection gain of 10 mV/A when used with a 200 Ω shunt resistor.
It is also important to ensure a symmetrical layout between the two phases in order to balance the phase current and minimize any impact caused by gate drive delay, switch conversion speed, overshoot, or other parameter mismatches. When using GaN power devices for design, the internal vertical loop [2] method involves placing the decoupling capacitor near the FET and placing a sturdy grounding layer below it. The microcontroller selected for this application has a high-resolution PWM module that can control the duty cycle and a dead time of 0.25 ns, allowing for optimization to fully utilize the performance of GaN FETs.
Both the step-down and step-up modes are controlled by the digital average current mode. The control block diagram is shown in the figure. 2. Use the same current reference I REF for two independent current loops to adjust the current in both inductors to the same value. The bandwidth of the two internal current loops is set to 6 kHz, and the bandwidth of the external voltage loop is set to 800 Hz.
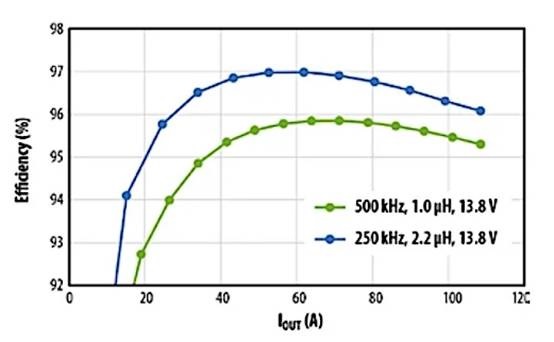
Figure 2: Digital average current mode control diagram
GaN FET requires a heat sink to operate at a full output power of 1.5 kW. Use standard commercially available 1/8 brick radiators. Four metal gaskets are installed on the PCB to provide appropriate clearance for the installation of the heat sink. An electrically insulating thermal interface material (TIM) with a thermal conductivity of 17.8 W/mK was applied between FET and heat sink.
Performance analysis
Figure 3 shows a photo of the EPC9137 [5] converter. After installing the heat sink and 1700 LFM airflow, the converter operates at 48 V input and 13.8 V output, and is tested at 250 kHz and 500 kHz.
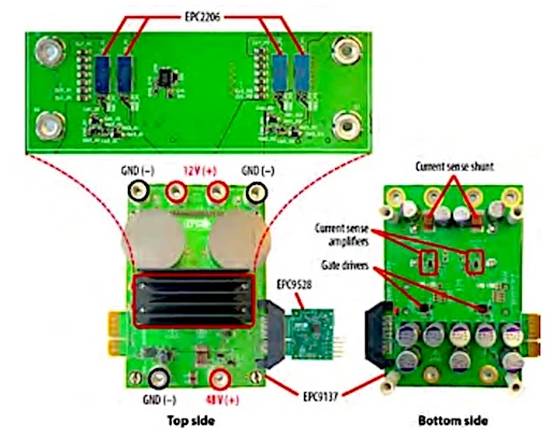
Figure 3: Photo of EPC9137 converter with EPC2206 GaN FET.
Figure 4 shows the efficiency results. At a frequency of 250 kHz, using a 2.2H inductor, the converter achieved a peak efficiency of 97%. When using a 1.0 H inductor to operate at a frequency of 500 kHz, the peak efficiency is 95.8%.
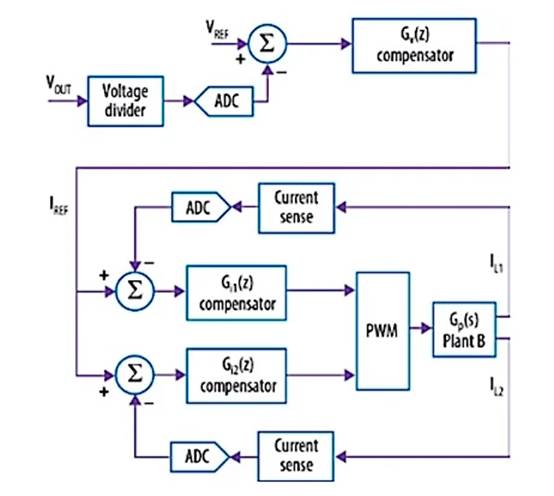
Figure 4: Efficiency of EPC9137 converter measured at 250 kHz and 500 kHz, 48 V input and 13.8 V output conditions.
The EPC9137 converter was also tested in boost mode operation with 13.8V input and 48V output, as shown in Figure 5.
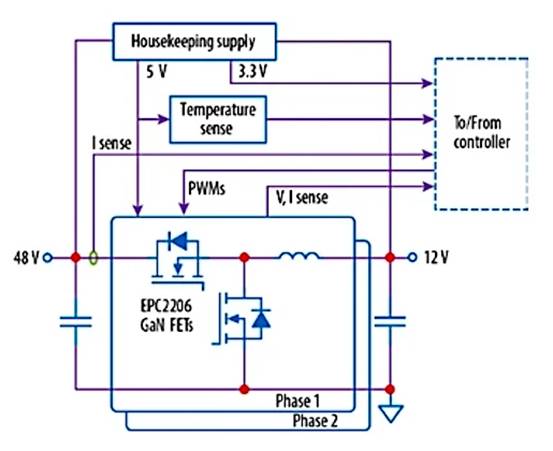
Figure 5: Efficiency of EPC9137 converter measured under 250kHz, 13.8V input and 48V output conditions.
At full load, the EPC eGaN FET can operate with 96% efficiency at a switching frequency of 250 kHz, achieving 750 W/phase compared to silicon-based solutions, while silicon-based solutions are limited to 600 W/phase due to inductor current limitations of 100 W/phase. KHz switching frequency.
conclusion
Automobile manufacturers are facing the requirement of accelerating the pace of vehicle electrification, competing in the market while also meeting increasingly stringent environmental legislation. This design example of a bidirectional DC-DC converter demonstrates how EPC‘s automotive grade eGaN FET (such as EPC2206) helps integrate a 48 V bus to power high-power loads and meet the growing power demands of the entire vehicle. When transmitting power between the 48 V and 12 V domains, the EPC9137 converter can achieve an efficiency of over 96% at a 250 kHz switching frequency and over 95% at a 500 kHz switching frequency.
Disclaimer: This article is transferred from other platforms and does not represent the views and positions of this site. If there is any infringement or objection, please contact us to delete it. thank you! |