Design considerations for heat dissipation in Class D power amplifier IC applications
Time:2024-02-12
Views:303
Class D amplifiers have higher efficiency and better thermal performance compared to Class AB amplifiers. However, when using Class D amplifiers, it is still necessary to carefully consider their heat dissipation. This application note analyzes the thermal performance of Class D amplifiers and illustrates the principles that should be followed for good design through several common examples.
Continuous sine waves and music
When evaluating the performance of Class D amplifiers in the laboratory, continuous sine waves are often used as the signal source. Although using sine waves for measurement is more convenient, such measurement results are the thermal load of the amplifier in the worst-case scenario. If a Class D amplifier is driven by a continuous sine wave near the maximum output power, the amplifier often enters a thermal shutdown state.
Common audio sources, including music and speech, often have RMS values much lower than peak output power. Normally, the peak to RMS power ratio (i.e. peak factor) of speech is 12dB, while the peak factor of music is between 18dB and 20dB. Figure 1 shows the waveform of audio signals and sine waves in the time domain, and presents the results of measuring the RMS values of both using an oscilloscope. Although the peak value of the audio signal is slightly higher than that of a sine wave, its RMS value is only about half of that of a sine wave. Similarly, there may be abrupt changes in the audio signal, but as measured, its average value is still much lower than that of a sine wave. Although audio signals may have peaks similar to sine waves, the thermal effect exhibited by Class D amplifiers is significantly lower than that of sine waves. Therefore, when measuring the thermal performance of the system, it is best to use actual audio signals instead of sine waves as the signal source. If only sine waves can be used, the obtained thermal performance will be worse than the actual system.
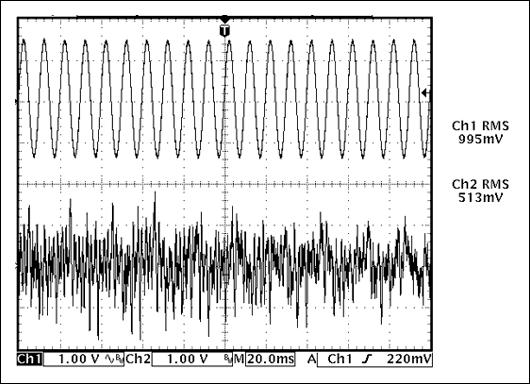
Figure 1. The RMS value of the sine wave is higher than the RMS value of the audio signal, which means that when tested with sine wave, the heating of Class D amplifier is greater (click to enlarge the image)
Precautions for PCB heat dissipation
In industrial standard TQFN packaging, exposed solder pads are the main way for IC heat dissipation. For packages with exposed solder pads at the bottom, the PCB and its copper layer are the main heat dissipation channels for Class D amplifiers. As shown in Figure 2, when mounting a Class D amplifier onto a common PCB, it is best to follow the following principle: solder the exposed solder pads onto a large area of copper blocks. Try to place more copper covering between the copper block and adjacent Class D amplifier pins with equal potential, as well as other components. In the case of this article, the copper layer is connected to the upper right and lower right of the heat dissipation pad (as shown in Figure 2). The copper wiring should be as wide as possible, as this will affect the overall heat dissipation performance of the system.
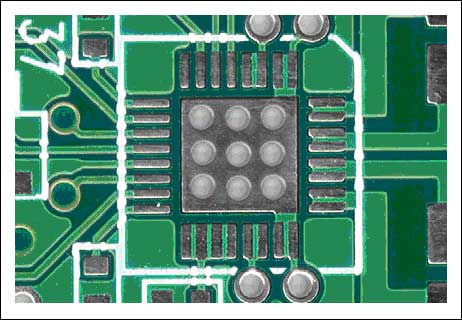
Figure 2. When Class D amplifiers are packaged in TQFN or TQFP, the exposed solder pads are the main heat dissipation channel
The copper blocks connected to the exposed solder pads should be connected to other copper blocks on the back of the PCB using multiple through holes. The copper block should have the largest possible area while meeting the requirements of system signal wiring.
Try to widen all connections with the device as much as possible, which will help improve the system‘s heat dissipation performance. Although the pins of the IC are not the main heat dissipation channel, there may still be a small amount of heat generation in practical applications. In the PCB shown in Figure 3, a wide connection is used to connect the output of the D-class amplifier to the two inductors on the right side of the figure. In this case, the copper core winding of the inductor can also provide additional heat dissipation channels for the D amplifier. Although the overall thermal performance improvement is less than 10%, such improvement will bring two completely different results to the system - even if the system has ideal heat dissipation or severe heat generation occurs.
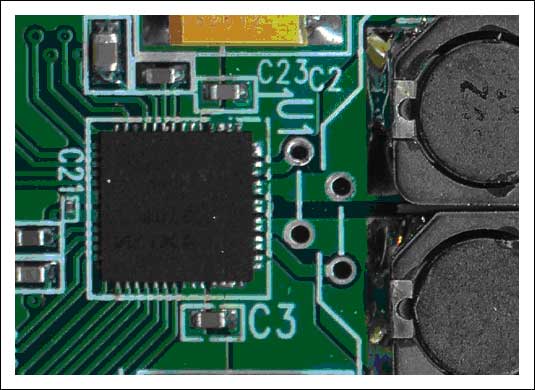
Figure 3. Wide wiring on the right side of Class D amplifier helps with thermal conductivity
Auxiliary heat dissipation
When Class D amplifiers operate at higher ambient temperatures, adding external heat sinks can improve the thermal performance of PCBs. The thermal resistance of the heat sink must be as small as possible to achieve optimal heat dissipation performance. After using bare solder pads at the bottom, the bottom of the PCB is often the heat dissipation channel with the lowest thermal resistance. The top of the IC is not the main heat dissipation channel for the device, so installing heat sinks here is not cost-effective. Figure 4 shows a PCB surface mount heat sink (218 series, provided by Wakefield Engineering). The heat sink is soldered onto the PCB, making it an ideal choice for balancing size, cost, assembly convenience, and heat dissipation performance.

Figure 4. When the Class D amplifier operates at higher ambient temperatures, the SMT heat sink shown in the figure may be required (image from Wakefield Engineering)
Thermal calculation
The core temperature of Class D amplifiers can be estimated through some basic calculations. In this example, the temperature is calculated based on the following conditions:
TAM=+40 ° C
POUT=16W
Efficiency ()=87%
JA=21 ° C/W
Firstly, calculate the power consumption of Class D amplifiers:
Based on these data, it can be inferred that the device has relatively ideal performance during operation. Because the system rarely operates at the ideal ambient temperature of 25 ° C, a reasonable estimate should be made based on the actual operating ambient temperature of the system.

Then, the temperature TC of the transistor core is calculated based on power consumption, using the following formula:

Load impedance
The conduction resistance of the output stage of Class D amplifier MOSFET can affect its efficiency and peak current capability. Reducing the peak current of the load can reduce the I2R loss of MOSFETs, thereby improving efficiency. To reduce peak current, the speaker with the maximum impedance should be selected while ensuring output power, voltage swing of Class D amplifier, and power supply voltage limitations, as shown in Figure 5. In this example, assuming the output current of Class D amplifier is 2A and the power supply voltage range is 5V to 24V. When the power supply voltage is greater than or equal to 8V, the load current of 4 will reach 2A, and the corresponding maximum continuous output power is 8W. If the output power of 8W meets the requirements, a 12 speaker and a 15V power supply voltage can be considered. At this time, the peak current is limited to 1.25A, and the corresponding maximum continuous output power is 9.4W. In addition, the work efficiency of 12 loads is 10% to 15% higher than that of 4 loads, reducing power consumption. The actual efficiency improvement varies depending on different Class D amplifiers. Although most speakers have an impedance of 4 or 8, other impedance speakers can also be used for more efficient heat dissipation.
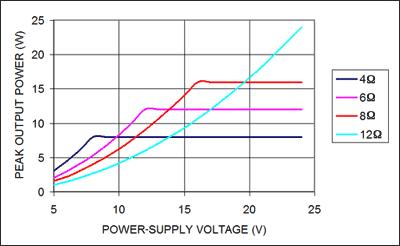
Figure 5. Selecting the optimal impedance and power supply voltage to maximize output power
Additionally, attention should be paid to the changes in load impedance within the audio bandwidth. A speaker is a complex electromechanical system with multiple resonant components. In other words, the speaker of 8 only exhibits 8 impedance in a very narrow frequency band. In most audio bandwidth, impedance will be greater than its nominal value, as shown in Figure 6. Within most audio bandwidth, the impedance of the speaker will be much greater than its nominal value of 8. However, the presence of high-frequency speakers and crossover networks will reduce impedance values. Therefore, it is necessary to consider the total impedance of the system to ensure sufficient current driving capability and heat dissipation performance.
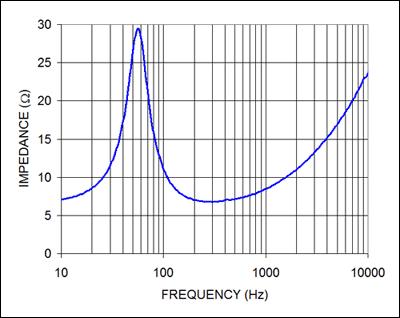
Figure 6.8 Impedance, the impedance of a 13cm caliber speaker changes sharply with frequency
Conclusion
The efficiency of Class D amplifiers is significantly improved compared to Class AB amplifiers. Although this efficiency advantage reduces the requirements for heat dissipation performance design in system design, system heat dissipation cannot be completely ignored. However, if good design principles can be followed and reasonable design goals can be set, using Class D amplifiers can make audio system design simpler.
Disclaimer: This article is transferred from other platforms and does not represent the views and positions of this site. If there is any infringement or objection, please contact us to delete it. thank you! |