Fully protected half bridge power IC supports motor integrated inverter
Time:2024-01-02
Views:411
Electric motor drives consume nearly 50% of Europe‘s electricity. Therefore, governments around the world have established regulations and standards to ensure the most efficient consumption of electricity while minimizing the impact and interruption on the power grid. Variable speed drives (VSDs) are now very common in the industry because they can reduce energy consumption by up to 90% compared to old-fashioned constant speed induction motors [2], while also having additional advantages such as reducing motor size, improving dynamic performance, and reliability.
The development of standards such as IEC 61000 is aimed at supporting the power grid in terms of electrical equipment immunity and radiation, as the large inductive loads brought by motor drives can significantly affect the stability of the local power grid. In order to meet these standards, various technologies are adopted in the motor drive system, including active power factor correction (PFC), which modulates distortion waves back into sine waves to maximize the active power supply to the grid.
GaN improves performance and cost
Gallium nitride (GaN) is a wide bandgap semiconductor with outstanding characteristics compared to old silicon semiconductors, including the ability to increase switching speed by 20 times and power density by more than 3 times. Applying GaN power devices to PFC and inverter level motor drive systems can significantly reduce power loss and size, thereby achieving integration between inverters and motors. This article provides a detailed introduction to the reference design of a 400 W motor integrated inverter created by Navitas.
GaN FET does not have any reverse recovery charge and can achieve extremely fast switching speed. The switching loss is 4-5 times lower than that of silicon IGBT and MOSFET, and the total power loss is reduced by about 50%. The decrease in power means that the heat emitted by the device is reduced, which can reduce the size of the heat sink and even eliminate it in low-power drives. In 2021, the cost of machining aluminum for radiator grade reached a 13 year high, with a price of approximately $8 per kilogram. Therefore, minimizing radiator demand can significantly save on total system costs. In addition, due to the reduction in system weight, transportation costs have also been reduced.
The combination of extremely low switching loss and no reverse recovery provides new degrees of freedom for switching frequency and thermal design of VSD. The working conditions of integrated motor inverters are very difficult. In addition to vibration and strong magnetic fields, the ambient temperature may be quite high, making the cooling of power semiconductors difficult. Therefore, start with power switches that do not generate a large amount of current. Heat first.
Integration improves the efficiency, control, and robustness of motor drivers
GaNSense technology integrates the performance of GaN power supplies with driver, protection, and dynamic sensing functions, making it an ideal choice for high reliability motor drive applications. Optimized gate drive?? The dynamic circuit and related voltage regulators, as well as protection circuits such as over temperature and over current detection, have independent self-protection capabilities. All of these features are fully integrated, achieving excellent performance and reliability. The input signal can be controlled through simple digital signals, eliminating external components and reducing PCB area. This is very advantageous for compact motor drivers, as the complete electronic system can be installed in the motor housing.
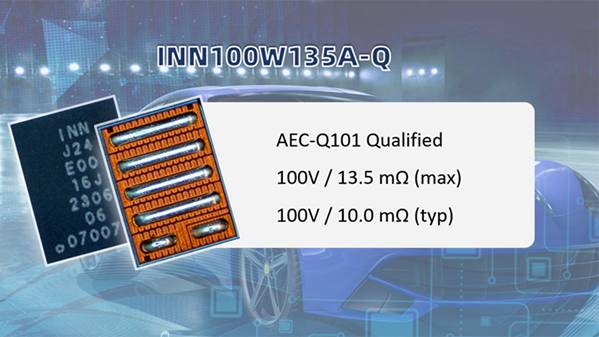
Figure 1 Simplified block diagram of fully integrated GaNFast IC using Navitas GaNSense technology. Image provided by Boduo Power System [PDF]
Compared to discrete silicon or discrete GaN methods, GaNSense? The technology only requires 30 ns to detect and protect, which is 6 times faster than silicon or split GaN, thereby improving system level reliability. For more detailed information, please refer to the application note AN015.
Compared to traditional high-precision temperature sensors on heat sinks, the temperature control integrated on the power switch can provide higher accuracy and real-time sensing. This is crucial for motor integrated drive applications that are difficult to maintain, especially in industrial environments where reliability and normal operating time are required. The built-in over temperature protection circuit will turn off the GaN IC when the set temperature is exceeded, thereby achieving rapid protection of the system.
The advantage of non-destructive current sensing in GaNSense technology eliminates the need for large and expensive shunt resistors, significantly reducing system size and cost while maintaining fast overcurrent protection to achieve the system robustness required for industrial motor drives in factory automation.
In addition, the total number of components has decreased, significantly reducing the FIT (timely failure) rate and improving system reliability. Navitas recently announced a 20-year limited warranty for its products, which is the first in the industry and highlights its outstanding reliability.
Navitas is launching a full range of GaN power ICs with half bridge topology, as shown in Table 1. Due to the existence of multiple GaN power half bridge ICs with different RDSON values and pin compatibility, this design can be easily expanded or power reduced.
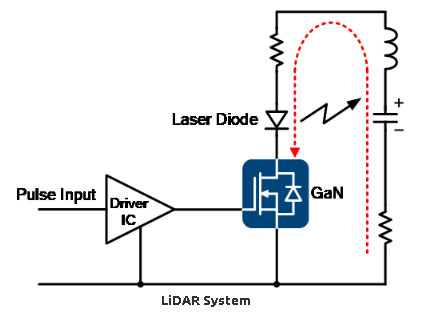
Table 1 The GaN power IC product portfolio for Navitas half bridge topology
NV6247 Half Bridge 650800160/160PQFN 6x8 Production
NV6245C Half Bridge 275/275PQFN 6x8 Project
All new half bridge products adopt space saving PQFN packaging, which can achieve good thermal connection with PCB, low parasitic inductance and resistance, and demonstrate the same robustness and reliability as Navitas single power switch, especially high transient voltage capability (650V continuous, 800V transient). They enjoy a nearly announced 20-year warranty. For more information on product performance and robustness, please refer to their respective data sheets [3] and dedicated application instructions AN-018 on www.navitassemi.com [5].
Reference Design for Motor Integrated Inverter
The availability of GaN power ICs in a half bridge topology enables the implementation of very compact motor inverters, as shown in Figure 2.
This inverter consists of three half bridge GaN power ICs (new NV6247) from Navitas. It includes input logic, level converter, voltage regulator and gate driver, current and temperature detection circuit, and bootstrap power supply. Therefore, the number of external components is very small.
The schematic diagram of one of the three branches of the inverter is shown in Figure 3. The second phase circuit is shown, and all three phases are the same. The main component is NV6247, which integrates two power switches in a half bridge configuration, a gate driver and its regulator, and an input logic labeled "PWM". The built-in bootstrap circuit is used to provide gate drive power to the high side driver. It also includes a level converter so that the input signal can be grounded as a reference, making the device a truly digital controllable power stage.
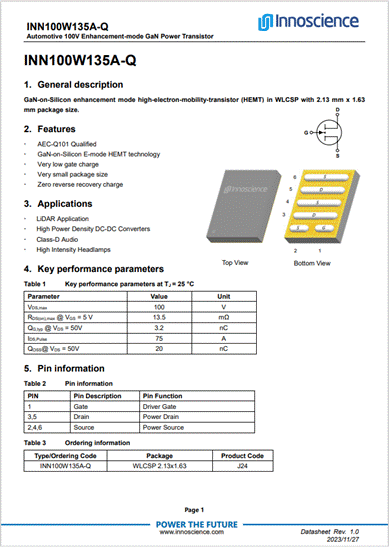
Figure 2 A circular PCB with a 400W motor inverter power stage, connected to the back of the BLDC motor, with a diameter of 56mm. Image provided by Boduo Power System [PDF]
In addition, it also includes various sensing functions. Firstly, the current flowing through the internal low side GaN power FET is sensed internally, and then converted at the current sensing output pin (CS)?? For current. Secondly, the junction temperature is sensed through the circuit on the gate driver and used to turn off the power switch in case of overheating.
The IC pins include the drain (VIN, connected to VBUS) of the high side GaN power FET, the half bridge midpoint switch node (VSW, connected to PHB), the source and IC GND (PGND) of the low side GaN power FET, the low side IC power supply (VCC), the low side gate drive power supply (VDDL), the low side conduction dV/dt control (RDDL), the low side 5V power supply (5VL), the low side reference PWM input (INL, INH), and the low side current detection output (CS) Automatic standby enable input (/STBY), high side power supply (VB), high side gate drive power supply (VDDH), and high side 5V power supply (5VH). The external low side components around the IC include a VCC power capacitor (CVCC) connected between the VCC pin and PGND, a VDDL power capacitor (CVDDL) connected between the VDDL pin and PGND, a conducting dV/dt setting resistor (RDDL) pin and RDDL pin connected between the VDDL, and a current detection amplitude setting resistor (RSET) connected between the CS lead and PGND, Connect the 5V power capacitor (C5VL) between the 5VL pin and PGND, as well as the automatic standby enable pin (/STBY) connected to PGND to enable automatic standby mode or to disable automatic standby mode when connected to the 5VL. The external high side components around the IC include a VB power capacitor (CVB) connected between the VB pin and VSW, a VDDH power capacitor (CVDDH) connected between the VDDH pin and VSW, and a 5V power capacitor (C5VH) connected between the 5VH pin and VSW. High side VB, 5VH, and VDDH bypass capacitors must be carefully selected to accommodate various system considerations, such as high side wake-up time, high side hold time, and standby power consumption. On the right side, you can see the VBUS blocking cap, and the PCB allows the use of thin film or electrolytic caps. Their purpose is to suppress any type of ringing that may occur due to parasitic inductance in power and switch actions, as the board is designed for DC input., R17 and C18 can be used to suppress ringing on switch nodes, as it may be caused by long cables and their inductance, and is optional.
It is worth noting that the switching speed of the power switch can be adjusted through an external resistor (R7 in this case). Although reducing switch speed does increase switch losses, the impact is not significant as switch losses are already very low. In this way, the switch speed can be adjusted according to the needs of the motor, and the generated EMI can be adjusted to comply with all required regulations, and the size of the EMI filter component can be reduced. A value of 50 Ω is a good starting point.
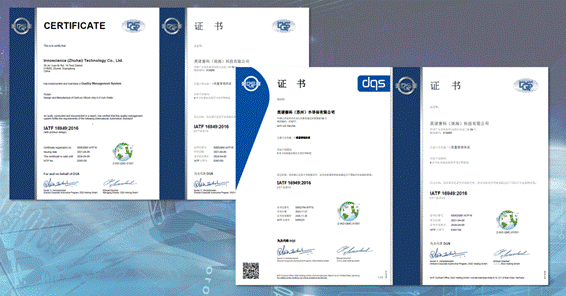
Figure 3 The schematic diagram of one of the three inverter branches shows that apart from the GaN power IC, only a few external components are required. Image provided by Boduo Power System [PDF]
The resistor on the CS pin (R8) can be set according to the needs of the microcontroller and its ADC input to appropriately scale the voltage. However, if the voltage on this pin exceeds 1.9V, overcurrent protection will be triggered. It should be noted that the selection of resistance on the CS pin will affect the voltage corresponding to the current in the power stage and overcurrent protection.
The automatic standby mode is designed to reduce the power consumption of NV6247 when not switched. If it exceeds about 90? If no more input pulses are detected within s time, the IC will automatically enter low-power standby mode. This will disable the gate driver and other internal circuits, and reduce the VCC power supply current to a lower level. When the INL pulse restarts, the IC will wake up after a delay in the rising edge of the INL input (usually about 450ns) and enter normal operating mode again.
Disclaimer: This article is transferred from other platforms and does not represent the views and positions of this site. If there is any infringement or objection, please contact us to delete it. thank you! 矽源特科技ChipSourceTek |