What is feeling, What is insensitivity,The difference between inductive and non inductive brushless DC motors
Time:2023-10-09
Views:628
What is feeling?
In sensorless brushes, sensing refers to "Hall sensors", so what is "Hall"? Hall refers to the Hall effect, which was discovered by American physicist A.H. Hall (1855-1938) in 1879 while studying the conductive mechanism of metals.When a current passes through a conductor perpendicular to an external magnetic field, there will be a potential difference between the two end faces of the conductor perpendicular to the magnetic field and the direction of the current, which is known as the Hall effect.This potential difference is also known as the Hall potential difference. Simply put, through Hall sensors, the brushless driver can clearly know the position of the rotor of the brushless motor.
What is insensitivity?
The term ‘senseless‘ in sensorless brushless refers to‘ no Hall sensor ‘,In the absence of direct feedback, the sensorless brushless motor can only obtain the rotor position of the motor indirectly. Common methods include back electromotive force method, inductance method, magnetic linkage method, high-frequency pulse method, and other intelligent methods, with back electromotive force method being the most commonly used.
When starting a sensorless brushless motor, because the rotor magnetic pole orientation is not known, it can only randomly change the current to drive the motor. Similar to "meng", there will always be a time when the rotor will roll, and after the rotor rolls, it can calculate the rotor‘s position by changing the current on the coil, and then control the current and direction. This is why there is always a "clicking" symptom when starting without feeling or brushing.
Unlike inductive brushless, with sensors, the driver knows the orientation of the rotor magnetic poles from the moment it starts up, and can directly supply the corresponding current to the corresponding coil to drive the rotor. But when the current is very low, the motor will make a continuous "squeaking" sound. This is why the induction motor will hear a continuous "squeaking" sound at low speeds, while the sensorless brushless motor will not.

Internal structure diagram
Advantages and Disadvantages of Sensory Brushless
Advantages: The motor has better linearity, strong speed stability, and high responsiveness.
Disadvantages: High cost and difficulty in waterproofing. Due to the limitations of Hall sensors, they are prone to interference, causing the driver to receive incorrect information and resulting in malfunctions. Therefore, the wire length from the driver to the motor is generally limited to less than 5 meters.
Advantages and Disadvantages of Senseless and Brushless
Disadvantages: Linearity is not as good as inductive brushless motors, and in addition, drivers on the market may have an error of more than ± 20 revolutions due to lack of accurate feedback on speed. Starting with load or full load is prone to shaking or starting failure.
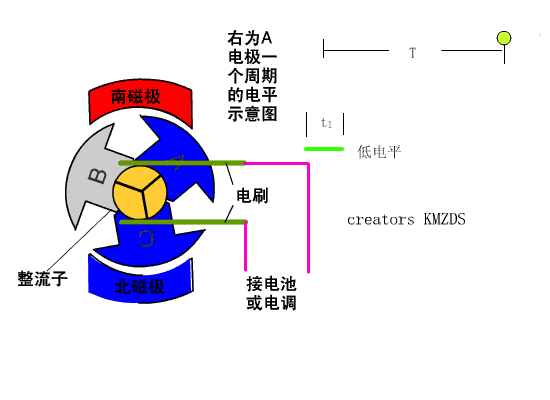
The difference in speed control methods between brush motor and brushless motor
In fact, the control of both types of motors is voltage regulation, but due to the use of electronic commutation in brushless DC, digital control is necessary to achieve it. Brushed DC is controlled through carbon brush commutation, which can be controlled using traditional analog circuits such as thyristor, making it relatively simple.
1. The speed regulation process of a brush motor is to adjust the voltage of the motor power supply. The adjusted voltage and current are converted through commutators and brushes to change the strength of the magnetic field generated by the electrodes, achieving the goal of changing the speed. This process is called variable voltage speed regulation.
2. The process of brushless motor speed regulation is to keep the voltage of the motor‘s power supply unchanged, change the control signal of the electrical regulation, and then change the switching speed of the high-power MOS transistor through the microprocessor to achieve speed change. This process is called variable frequency speed regulation.
Disclaimer: This article is transferred from other platforms and does not represent the views and positions of this site. If there is any infringement or objection, please contact us to delete it. thank you! |