Battery safety, chip responsibility
Time:2023-10-06
Views:658
Author: Doctor M
Driven by the trend of electrification, cars are undergoing earth shattering changes, with the core three major components changing from the engine, chassis, and gearbox of fuel powered vehicles to the "three electric systems" of electric vehicles - electric drive, battery, and electronic control. According to cost data released by car companies, the battery system is the most expensive component in electric vehicles, accounting for nearly 40% of the total cost.
On the one hand, the battery system of electric vehicles cannot afford to malfunction. In the maintenance project of electric vehicles, once linked to the battery system, the maintenance cost will skyrocket. Including the component premium of the maintenance system, once the battery system malfunctions, it often requires maintenance at a cost of nearly 60% of the entire vehicle price. On the other hand, occasional electric vehicle spontaneous combustion accidents have proven that electric vehicle battery detonation has greater destructive power and leaves shorter escape time for drivers and passengers. Therefore, ensuring the safety and stability of the battery system is a common goal of the entire electric vehicle industry.
In fact, since the explosion of mobile phones and electric bicycles, the public and industry have been paying attention to the safety issues of lithium batteries. However, in the automotive field, the concept of safety has been further strengthened. In this article, we will provide a specific explanation of the safety protection of lithium batteries and recommend components distributed by Maoze Electronics that can ensure battery safety.
About Lithium Battery Safety
As is well known, lithium batteries have considerable danger due to their physical characteristics. When charging a lithium battery, it converts electrical energy into chemical energy for energy storage, and when discharging, it converts chemical energy into electrical energy for energy release. Once lithium batteries store energy, uncontrolled energy release can cause detonation. Due to the pursuit of long range in smartphones, electric automatic vehicles, and electric vehicles, the high energy density of battery systems has become a product advantage, but this actually further increases the destructive power of detonation.
Of course, the ultimate destructive power of lithium batteries is presented through deflagration, but this is not instantaneous, but a gradual process in the form of thermal runaway. What situation can cause thermal runaway of lithium batteries? The industry collectively refers to these situations as abuse conditions. After reviewing the Chinese national standard GBT31485-2015 "Safety Requirements and Experimental Methods for Power Batteries Used in Electric Vehicles", it was found that abuse conditions include over discharge, overcharging, internal and external short circuits, squeezing, and dropping.
Taking the power battery system of electric vehicles as an example, it generally consists of battery cells, BMS (battery management system), structural components (box, wires, connectors, etc.), and thermal management system.
A battery cell is a single cell lithium-ion battery, consisting of a positive electrode, negative electrode, separator, electrolyte, and structural components. Many power battery system accidents, such as spontaneous combustion, are caused by short circuits within the battery cells. After an internal short circuit occurs, the temperature of the battery cell will rapidly rise. When the temperature reaches a certain level, the diaphragm that protects the negative electrode active material inside the battery cell will disappear, causing the negative electrode to be completely exposed. The electrolyte will decompose and release a large amount of heat on the electrode surface, which is the first step in a series of exothermic side reactions that occur inside the battery. Then a large amount of heat and combustible gases are released, ultimately causing the system to explode.
In addition, there are two types of abuse that can cause battery system detonation: high temperature and overcharging. High temperature also includes rapid system temperature rise caused by over discharge and external short circuits, which are the focus of BMS system monitoring. BMS is responsible for monitoring battery terminal voltage, energy balance between batteries, total battery pack voltage/current, battery terminal/battery pack temperature, etc. As mentioned above, when these indicators undergo abnormal changes, the battery will enter an abuse condition. If not stopped in a timely manner, it can cause a detonation accident.
Electric vehicles have an urgent demand for high-performance BMS. At the same time, the rapid growth of the electric vehicle market also has a positive driving effect on BMS products. According to the analysis data of QYReasearch, the global automotive BMS market size reached 21.7 billion yuan in 2020, and it is expected to reach 88.5 billion yuan in 2027, with a compound annual growth rate (CAGR) of 26.19%.
BMS is often referred to as a "battery nanny" or "battery butler" by many businesses. Its main function is to intelligently manage and maintain various battery units, prevent overcharging and discharging, extend battery life, and monitor battery status. In terms of battery management, BMS can accurately obtain the State of Charge (SOC) of the power battery pack, ensuring that SOC is maintained within a reasonable range, and preventing damage to the battery due to overcharging or discharging. When the voltage or capacity of certain batteries in the battery pack is found to be too high/too low, BMS has the ability to balance between individual batteries, which is a key step in preventing battery cells from entering abusive situations. This not only prolongs the system life, but also eliminates safety risks, while providing safe and stable operating conditions for fast charging.
In summary, in the application of electric bicycles and electric vehicles, the BMS system mainly achieves the following functions:
·Accurately obtain the SOC of the power battery pack and maintain it within a reasonable range through system algorithms;
·Balanced management of battery packs and cells, including thermal management, charge and discharge management, etc;
·Provide multiple protection functions for the battery pack, including overcharge protection, over discharge protection, short circuit protection, etc;
·Utilize communication bus and vehicle system for information exchange.
In addition to innovating in key technology areas such as BMS and battery materials, in order to promote the safe use of lithium batteries, policies are also accelerating the issuance of relevant regulations, striving to provide correct guidance for the industry.
LTC3300
Multi cell battery balancer for electric vehicles
In the above analysis, we took the automotive power battery system as an example to explain which abuse situations can lead to the risk of detonation of the power battery pack, and mentioned the important role of the BMS system in the safety aspect of the power battery system. Next, the first product we will introduce is the LTC3300 multi cell battery balancer that can be applied to the BMS system of electric vehicles. This product is supplied by manufacturer ADI, and the supplier‘s product number on Maoze Electronics is LTC3300HLXE-2 # WPBF.
The LTC3300 bidirectional multi cell battery balancer is a fault protection controller IC suitable for transformer based bidirectional active charge balancing of multi cell battery packs. From Figure 1, it can be seen that the LTC3300 has rich pin functions, integrating various related gate drive circuits, high-precision battery sensing, fault detection circuits, and a robust serial interface with a built-in watchdog timer inside the device.
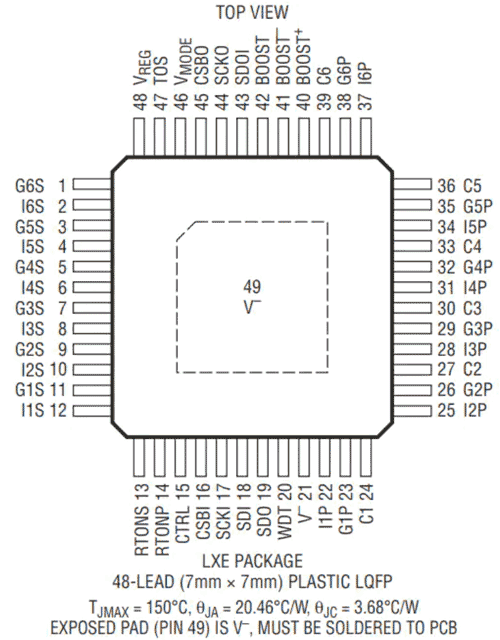
Figure 1: LTC3300 Pin Configuration (Image Source: ADI)
Figure 2 is a typical application diagram of LTC3300. This device can balance the charge of up to 6 series connected batteries using an input common mode voltage of up to 36V, solving the inefficient problem of unidirectional balance when the battery voltage in the battery pack is very low, thereby achieving charge balance for each battery in a long series connected battery. Minimize balancing time and reduce power consumption as much as possible. Through external settings, the balance current can reach 10A.
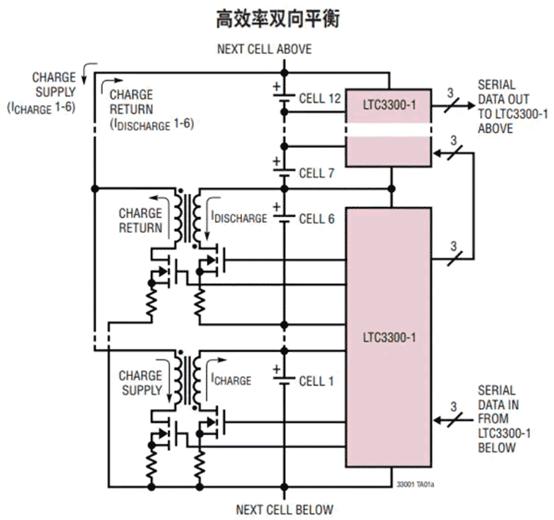
Figure 2: Typical Application Block Diagram of LTC3300 (Source: ADI)
At the same time, the LTC3300 has industry-leading scalability. With its level conversion SPI compatible serial interface, it can complete the series connection of multiple LTC3300-1 devices without using optocouplers or isolators, and can stack and support systems above 1000V. And the LTC3300-1 connected in series can work simultaneously, so it can independently balance the charge of all batteries in the battery pack simultaneously. In addition, the LTC3300 can be seamlessly integrated with the LTC680x series multi cell battery stack monitor.
As shown in Figure 3, the LTC3300 has a balancer efficiency of up to 92%.
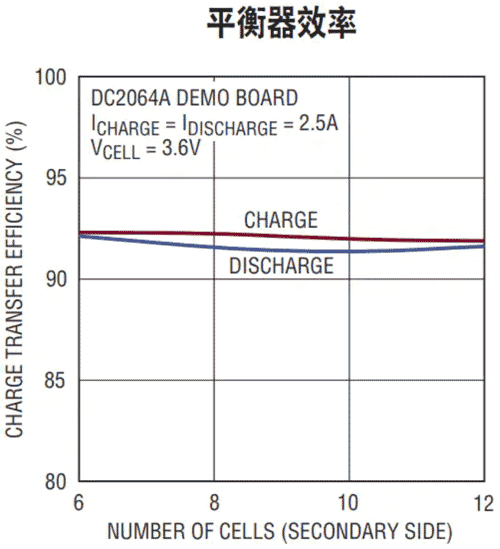
Figure 3: Measured Efficiency of LTC3300 (Source: ADI)
The comprehensive and excellent protection performance is a major highlight of the LTC3300 device, which can provide various fault protection features, including read back capability, cyclic redundancy check (CRC) error detection, maximum on-time volt second clamping, and overvoltage shutdown.
When applied to BMS systems for series connected lithium-ion batteries, the battery pack balancer composed of LTC3300-1 is a key component in the system, capable of working in conjunction with monitors, chargers, microprocessors, or microcontrollers. Figure 4 is the schematic diagram of LTC3300-1 applied to the BMS system. The function of the battery pack balancer in the system is to transfer charge between a given unbalanced battery and adjacent larger battery packs (including unbalanced batteries) to achieve voltage or capacity balance between a single battery and the entire battery pack.
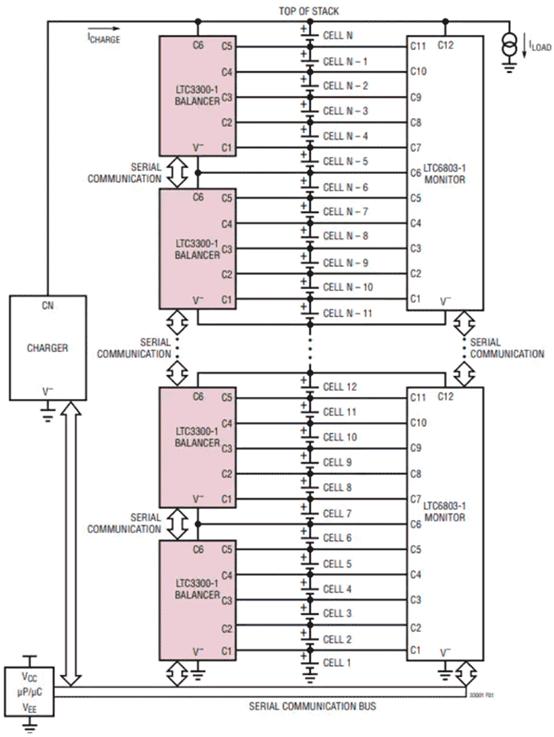
Figure 4: Schematic diagram of LTC3300-1 applied to BMS (source: ADI)
In the BMS system, the seamless integration of LTC3300 and LTC680x series multi cell battery stack monitors provides high-precision voltage monitoring protection. The balancing efficiency of up to 92% allows the LTC3300 to more than double the balancing current compared to solutions with the same balancer power consumption and an efficiency of only 80%.
This efficient balancing method extends the service life of the power battery pack and helps achieve faster charging speed. From a system security perspective, more efficient battery balancing can avoid worsening the situation. When there is an imbalance in battery cell voltage or energy, if it cannot be quickly resolved, it is easy to further deteriorate into overcharging or discharging, which is the abuse situation we mentioned above.
In potential application scenarios, LTC3300 can be applied not only to BMS systems for electric vehicles or plug-in hybrid vehicles (HEVs), but also to battery pack monitoring for universal multi cell batteries, high-power UPS/grid energy storage systems, and other markets.
ISL94216x
Accurate monitoring of battery front-end IC
In the above content, we have repeatedly mentioned the important role of BMS in electric vehicles and introduced a component that can be used for balancing BMS batteries in electric vehicles. In fact, the BMS system is also extremely important in the field of electric bicycles. Frequent accidents have prevented electric bicycles from entering residential buildings, but to prevent such accidents, it is still necessary to fundamentally improve the battery safety of various types of light electric vehicles.
Next, this device can be used for the BMS system of light electric vehicles, which is the ISL94216x battery front-end IC from manufacturer Renesas Electronics. Engineer friends can accurately locate the manufacturer‘s device number ISL94216IRZ by searching for it on Maoze Electronics.
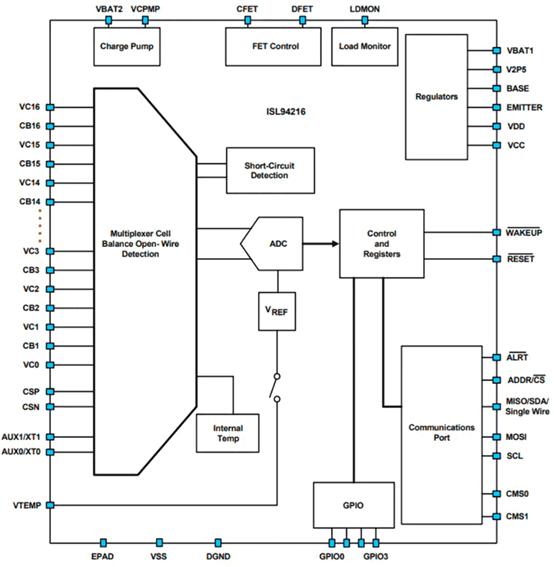
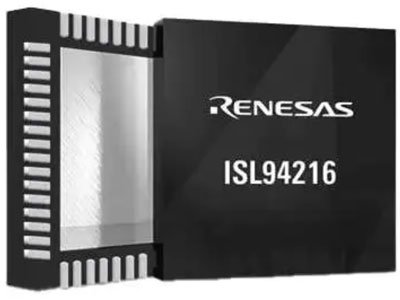
Figure 5: ISL94216x Battery Front End IC (Image Source: Renesas Electronics)
Figure 6 is the system diagram of the ISL94216x battery fr
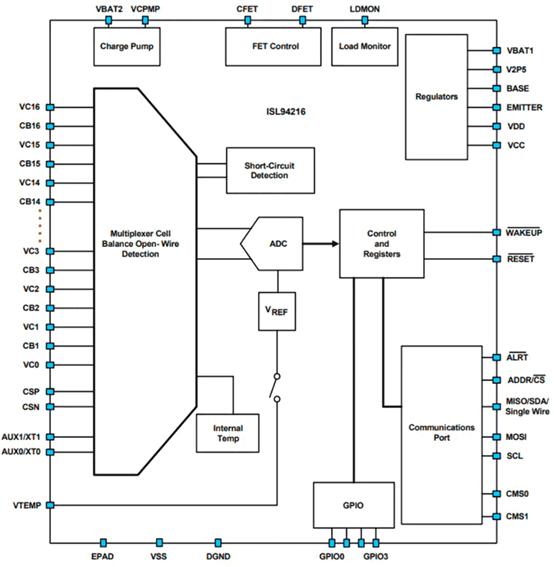
Figure 6: ISL94216x Battery Front End IC System Block Diagram (Source: Renesas Electronics)
The ISL94216x battery front-end IC has multiple battery monitoring functions, which can regularly scan the battery status and working environment to optimize battery life and prevent catastrophic failures. The differential multiplexer and 16 bit ADC equipped with this device can accurately monitor the battery voltage, temperature, and load current under the overall state of the battery pack. At the same time, the charging/load wake-up detection circuit in the device can dynamically obtain the working status of the battery pack.
The core functions of the BMS system are monitoring and balancing. In terms of battery balance, the ISL94216x battery front-end IC has an internal battery balance circuit that can provide a balanced current of 8mA per section. Therefore, when applied to the BMS system of light electric vehicles, this device can provide multiple operating modes and monitoring/protection functions.
Here, we would like to emphasize the open circuit detection function of the ISL94216x battery front-end IC. The circuit diagram is shown in Figure 7, where VC0-VC16 checks the wire between the connector and the battery (blue), and VSS and VBAT1 OW check the red connection to determine whether the BMS and battery unit are disconnected.
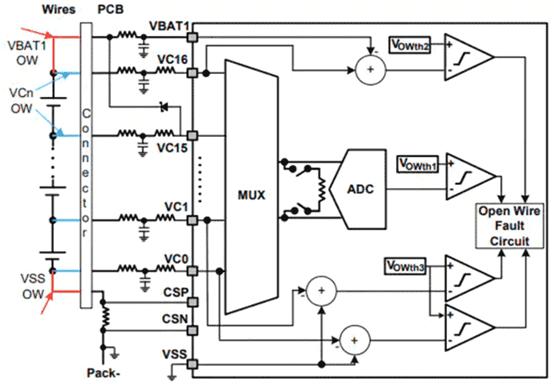
Figure 7: ISL94216x Battery Front End IC Open Circuit Detection Function (Image Source: Renesas Electronics)
Open circuit detection is a very important function in BMS self diagnosis. Once the connector and battery pack are disconnected, the BMS will no longer be able to provide system monitoring and adjustment functions. If other circuits continue to work at this time, it will not only damage the battery pack, but also cause accidents.
Nip danger in the bud
From the current technological status of the industry, the inherent risks of lithium batteries will continue to exist for a long time to come, but the industry is not helpless in this regard. From system monitoring to battery balance, the battery protection components provided by major manufacturers can nip the danger of lithium batteries in the bud.
The importance of the BMS system has been recognized by the entire industry. Facing the future, BMS needs better state estimation technology, battery diagnosis technology, and active balancing technology, and cloud BMS will also become an inevitable trend; In terms of product form, distributed management makes the functions of BMS clearer and more separate, and integrates them into different domain controllers through integration technology; Furthermore, BMS will pursue more advanced functional safety and achieve safety management throughout the entire battery life cycle; In addition, low-cost technology is the main implementation method for future BMS.
Of course, electronic components are the cornerstone of achieving all of this. And these components with excellent protective performance can be easily obtained by engineers under the "Battery Management" section of Maoze Electronics, and there are rich development tools associated with the components to help engineers ensure the "safety" of lithium battery applications.
Disclaimer: This article is transferred from other platforms and does not represent the views and positions of this site. If there is any infringement or objection, please contact us to delete it. thank you! |