Simple open-circuit protection of boost converter
Time:2023-02-01
Views:1376
introduction
One way to drive high-brightness LED is to modify the standard boost converter topology to drive a constant current through the load. However, this implementation method has a serious problem because the open circuit fault in the LED string will remove the path of the load current. Due to the high output voltage from the converter (which operates without feedback at this time), this may cause potential damage to the circuit. This paper introduces a simple and robust open-circuit fault protection method, which uses a Zener diode and a resistor, and has a negligible impact on the total efficiency. We can verify the functionality of this topology by configuring a high-voltage boost converter as a constant-current driver to drive three high-brightness white LEDs and generate an analog fault state at the output end. The circuit controls the output voltage at a certain safe level and reduces the output current under the protected state.
Typical high-brightness LED boost converter
We often modify the converter to drive high-brightness LED in single-section lithium ion (Li-Ion), alkaline and other applications. In these applications, the voltage of the LED string exceeds the battery or power rail voltage. In the structure configuration of the high-voltage boost converter of the LED driver without open-circuit protection in the standard boost diagram 1, a voltage divider is used to generate the feedback voltage VFB of the circuit to monitor the output voltage VOUT. The converter adjusts the output voltage so that the VFB is always equal to the on-chip reference voltage VREF. This topology is adaptive. The upper resistor in the feedback voltage divider can be replaced by the load to maintain a constant current rather than a constant voltage, as shown in the LED string in Figure 1.
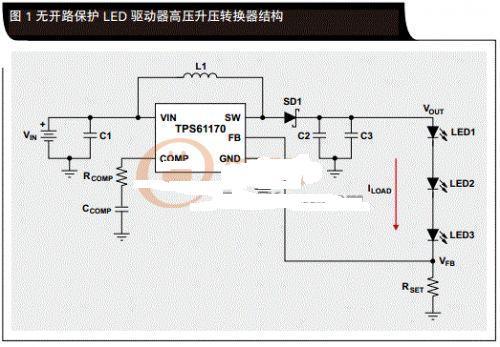
The load current depends on the on-chip reference voltage of the boost converter, and its calculation method is as follows:
.gif)
A serious problem with this simple implementation method is that the open circuit fault in the LED string will remove the path of the load current. When no current flows through the feedback resistor RSET, the VFB is pulled down to ground. In response, the boost converter will increase its duty cycle as much as possible to the maximum value in order to maintain the correct voltage on the feedback (FB) pin. The idealized boost converter transfer function shows that when the converter approaches its maximum duty cycle, it can produce high output voltage (VOUT). Consider a boost converter with a typical maximum duty cycle of 90% (common value) and 5V input:

The high voltage at the output end of the converter may cause multiple failures. This voltage may exceed the rating of internal or external switching devices or passive components. In addition, if the circuit is operated without protective measures, it will also bring potential danger to users and may damage the load during connection.
protection circuit
In case of open circuit, the load current must have a standby path. Although series-parallel connection of a resistor and LED can provide a path, it is not ideal because it will cause huge efficiency loss. The alternative configuration (Figure 2) is composed of a Zener diode and a resistor, which can provide sufficient system protection with minimal efficiency loss.
When the load current path is removed, the output voltage rises until Zener diode ZD1 is turned on, and the current flows through RPRO and RSET to ground. The output current is determined by the series combination of RPRO and RSET, because the VFB is equal to the internal bandgap reference voltage VREF after being driven. Therefore, the output protection current defaults to:
.gif)
We select a voltage for the Zener diode so that no current flows through it during normal circuit operation. In order to ensure that the LED driver circuit with open-circuit protection in Figure 2 is fully closed during normal operation, the selected voltage should be at least 2V higher than the maximum load voltage, but less than the specified maximum output voltage of the boost converter. In this way, circuit designers are not often forced to increase the rated voltage of output capacitors C2 and C3 and clamping diode SD1.3
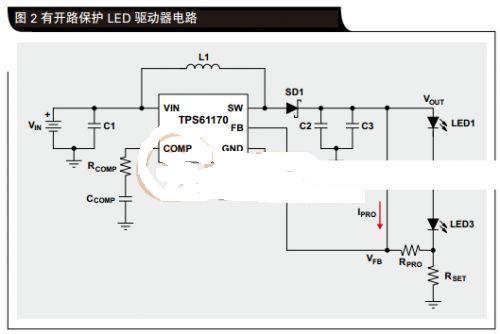
The output voltage is controlled as the sum of zener diode voltage and reference voltage:

The RPRO value is selected by balancing the LED current sensing error and power consumption during circuit protection. In fact, the value of RPRO should be as large as possible to minimize the power consumption of Zener diode:
The error entering the circuit is caused by the leakage current IZL of the Zener diode and the bias current IFB of the internal error amplifier of the boost converter. Equation 6 is a modified transfer function that includes these errors:
.gif)
Because these two currents are generally less than 1 μ A. Therefore, the error caused is very small and can be ignored in most implementations.
Demonstration demonstration
Figure 3 Screen capture of protection circuit activation oscilloscope as an application example, TI TPS61170 boost converter IC is configured as a constant current LED driver. In applications such as backlight lighting or flashlight, it is an ideal boost converter for driving high-brightness LED strings. The 3V-18V input range allows a wide power range, such as 2S to 4S lithium-ion or 3S to 12S alkaline battery pack, USB or 12V power rail.
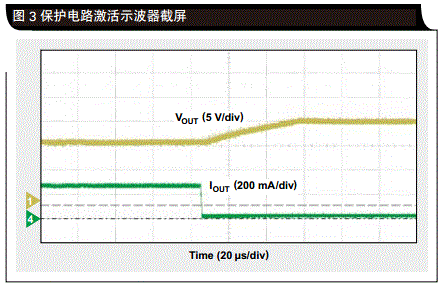
The boost converter is configured to drive three high-brightness white LEDs (260 mA). When the typical reference voltage is 1.229 V, the simplified load current is used in equation 7 to calculate RSET:

We choose 1mA value as the protection current (IPRO) to calculate the RPRO value:
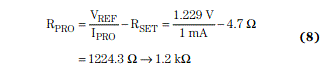
We select a 15V Zener diode for ZD1 to represent the minimum leakage current at the estimated load voltage of about 10V, and control the output at a value far lower than the maximum allowable output voltage (40V) of the boost converter. The output voltage is controlled at the zener diode voltage (VZD1), and its sum with the converter reference voltage is:

Using the selected load current and protective resistor, calculate the deviation from the expected load current (see equation 10 below). Data sheet value 200 nA for feedback bias current (IFB), 1 μ The value A is used for the predicted leakage current of Zener diode, and the VOUT is about 10V
The target load current of the circuit is 260 mA. As we can see, once the theoretical value of the components is replaced by the effective value in equation 10, the error caused by them will be far greater than the error caused by the protection circuit itself.
In order to test the operation of the protection circuit, we use a 38 Ω resistor decimal box to replace the LED string, in order to simulate the voltage of the LED string under the design load current. By quickly changing the load resistance from 38 Ω to 1038 Ω, an open circuit fault can be simulated. As shown in Figure 3, this change in output current (green line) indicates a sudden change in load impedance. To compensate, the output voltage (yellow line) of TPS61170 rises to reach the design load current again. However, this change will not always be the case until the maximum duty cycle is reached and the output voltage is stabilized at a clamping voltage of about 16V.
conclusion
We have introduced a simple method to provide open-circuit protection for the boost converter configured as a constant-current LED driver. This circuit consists of a Zener diode and an additional resistor, which limits the output voltage to a safe level and reduces the output current in the event of an open circuit fault in the load. In addition, this method brings some errors to the load current calculation process and slightly reduces the efficiency during normal circuit operation, but these effects can be ignored. Configure a boost converter as an LED driver, and add a 15V Zener diode and a 1.2k Ω resistor for output protection. This demonstrates the functionality of this protection circuit. This demonstration demonstrates that the output performance of the circuit under the simulated load fault state is in line with our expectations.
Disclaimer: This article is transferred from other platforms and does not represent the views and positions of this site. If there is any infringement or objection, please contact us to delete it. thank you! |