Simplify BLDC motor control design
Time:2022-06-06
Views:2127
By Miguel Mendoza
There is a growing trend from brush motor to brushless motor, especially in the development of energy-saving battery power supply system, because BLDC motor has many advantages over traditional brush motor. Although BLDC motors are more complex, we usually see higher power efficiency, less radiant heat and greater torque in smaller sizes without affecting robustness or reliability. Not to mention that there are no brushes to worry about replacing.
The new raj306000 series motor drive IC further simplifies the motor drive design by integrating the controller, power stage and power management module into one package. These motor drive ICs also provide additional functions, such as dual boost charge pump, BEMF detection circuit, current detection and self-aligned dead band (SADT) generator circuit. We specially designed the new raj306001 and raj306010 to reduce the BOM and overall circuit board size and improve the overall performance of the motor driver. The external MOSFET is used to allow the designer to select the appropriate power level for his system.
Bidirectional brush motor control circuit
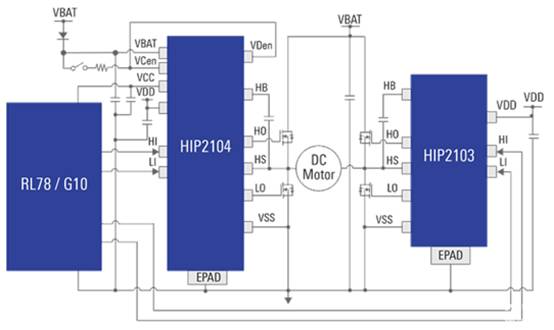
BLDC motor circuit using raj306001
The raj306000 series integrates rl78/gif MCU, enabling us to utilize the motor control firmware that has been used and verified in the market for many years. By providing software flexibility and enhanced hardware functionality, these motor drive ICs can support many different applications with different power and performance requirements.
For example, in wireless vacuum applications, a high speed is required to move a large amount of air to generate greater airflow and vacuum suction. In customer evaluation and our own tests, the raj306000 motor drive IC has driven unipolar motors up to 90K rpm.
In power tool applications, these devices support the complex motor control algorithms required by these systems. When the motor stops completely, the electric tool must be started under high torque conditions. They must also handle large load changes that require fast response times to maintain consistent RPMs.
Today, even low-cost, mass applications using 120 degree motor drive algorithms are turning to vector control and FOC drive. Because the raj306000 motor drive series has MCU, it can adapt to new trends and provide the latest available software.
Disclaimer: This article is transferred from other platforms and does not represent the views and positions of this site. If there is infringement or objection, please contact us to delete. thank you! |