Structure and working principle of integrated DC / DC converter
Time:2022-05-23
Views:2140
For smart card power supply, this paper proposes an integrated DC / DC converter structure and analyzes its working principle. The efficiency of the system can reach 85%, with sufficient robustness, which can meet all complex iso7816-3 specifications, and has passed EMV and EMV co procedures level 1 and level 2. The structure is especially suitable for smart card applications such as portable cash register (POS).
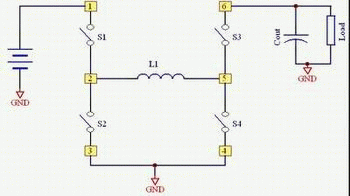
The operating voltage of the smart card has been upgraded to be suitable for any chip specifically for this application. The initial iso7816-3 and EMV (europay / Master Card / visa) documents now include 1.8V, 3.0V and 5.0V as applicable working power supply. Therefore, the physical interface between the card and must be able to adapt any of the above power supplies to the main MPU. The power supply must maintain the operating conditions specified in Table 1. In addition, the power supply must be able to operate at 750 μ Disconnect from the card within s, especially when the card is pulled out with power.
In addition to static operation, the power supply can keep the output voltage within the tolerance when the load is 100mA / 400ns pulse. Such requirements relate to the working state of the system, not just the power supply.
DC / DC converter
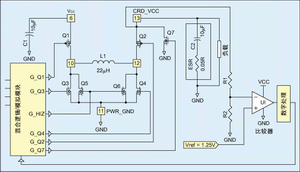
With the increasing application, from battery powered portable system to TV satellite receiver, smart card interface must deal with a large input voltage range and have high efficiency. Basically, it can be implemented in any type of structure as long as it can provide the required power for the card. For example, it can be designed as a switching capacitor based converter, but considering the portable POS system, its limited efficiency has become a key problem. For GSM applications, it is different. Because the output power is limited to 50MW, this capacitor based structure is preferred on the radiotelephone PCB to save space.
Considering that for the portable module of POS machine, energy saving is the key problem, so the structure based on inductance is given priority to improve the efficiency as much as possible. In fact, when the output power is up to 300MW, the efficiency of the inductor structure in the whole working voltage range can reach 85%, which is a level difficult to achieve by low-cost switched capacitor technology.
On the other hand, because the input voltage can be from 2.70v low to 5.50V high (after the battery is almost exhausted or after the battery is charged), the structure must automatically and without adjustment switch from boost to step-down, and vice versa. The concepts described in Figure 1 have been developed to meet these requirements and to maintain EMV as the main goal in the design.
The real system realized in silicon bare chip is more complex, because it can not have voltage spikes, but also realize adjustment and low ripple. It is important that the circuit meet all EMV specifications, especially the power down sequence, power off sequence and output short-circuit current.
To meet these requirements, the converter shown in Figure 2 adds several additional NMOS and PMOS transistors.
The system operates according to the concept of two cycles (see Figure 2 and figure 3 for all notes), and has a special structure considering the requirements of smart card:
Cycle 1: Q1 and Q4 are turned on, and inductor L1 is charged by external battery. At this stage, Q2 / Q3 and Q5 / Q6 are turned off.
The current flowing through Q1 and Q4 MOSFETs is internally monitored and turned off when it reaches the ipeak value (peak current, depending on the programmable output voltage value). At this point, cycle 1 is completed and cycle 2 begins. The "on" time is a function of the battery voltage and the inductance network values (L and Zr) connected between pins 10 and 11.
To prevent uncontrolled operation, 4 μ The s-pause structure ensures that the system operates only in a continuous cycle 1 loop under overload or low battery input.
Cycle 2: Q2 and Q3 are turned on, and the energy stored in inductor L1 is transferred to the external load through Q2. At this stage, Q1 / Q4 and Q5 / Q6 are turned off. The current flow cycle is a constant value of 900ns (typical value), if CRD_ If the VCC voltage is lower than the specified value, repeat cycle 1 after this period of time.
When the output voltage reaches the specified value (1.80v, 3.0V or 5.0V), Q2 and Q3 are shut off immediately to avoid Overvoltage on the output load. At the same time, two additional NMOS Q5 and Q6 are turned on to completely discharge the current stored in the inductor and avoid ringing and voltage spikes on the system. Figure 3 shows the theoretical waveform of DC / DC converter.
When CRD_ The VCC is programmed to 0V, or when the smart card is pulled out of the socket, the active pull-down Q7 quickly discharges the output energy storage capacitor to ensure that the output voltage is less than 0.40V when the card slides on the ISO contact. Due to the low on resistance of Q7, the output voltage is less than 100 μ It drops rapidly to 400mV within s, which is far lower than the maximum value of 750 specified by EMV μ s。
Output voltage ripple, although not directly specified by iso7816-3 or EMV, plays an important role in the operation of smart card. Its peak to peak value depends on the following two main electrical parameters:
1. Total series resistance between output silicon structure and net energy storage capacitor;
2. Voltage stabilization, that is, the ability to detect the output voltage with small threshold and lag.
The two parameters depend on the internal welding wire connecting the chip to the outside, the pin contact connecting the series resistance of the energy storage capacitor, and the printed copper wire used to connect the pin to the load. When a large current passes through the pin, the multi welding wiring technology is widely used to reduce the series resistance to 50m (, or if a wider welding wire is used, the resistance value is lower.
The width of printed circuit board routing can be determined according to the current processing needs of a given application. In addition, the series resistance can be a problem because the external passive components involved vary greatly with different applications. The key part is the energy storage capacitor, because (for economic reasons) it is generally a low-cost type, but this will produce high voltage spikes that can hardly be completely eliminated.
Depending on the type of technology used to develop capacitors, parasitic elements may have relatively high values and produce large uncontrollable spikes. As shown in Figure 4, this equivalent series resistance (ESR) is very easy to cause such spikes because the supply current flows directly through it and brings high-voltage pulses into the output source.
Based on the experiments carried out in the characterization of ncn6001 and ncn6004a, the best scheme is to use two parallel 4.7 μ F / 10V / ceramic / X7R capacitor to realize CRD_ VCC filtering. ESR does not exceed 50m? In the whole temperature range?, Moreover, the combination of standard components provides an acceptable tolerance of - 20% to + 20%, and the cost increase is limited. Table 2 gives a general comparison of common capacitor types. Figure 5 shows the CRDs observed on the ncn6001 or ncn6004a demo board for different capacitor types for output voltage filtering_ VCC ripple. The large and fast transients observed on the above curve are very difficult to filter out because of their high energy. Clearly, aluminum capacitors are not suitable for such applications and should be avoided.
The second parameter depends on the performance of the internal comparator, voltage reference tolerance and digital processing. The voltage reference is derived from a stable bandgap circuit with a tolerance of ± 3%. On the other hand, the deviation and drift of simulation function are reduced by high-end integration technology. Detailed analysis of DC / DC operation helps to understand the impact of each element on the output voltage ripple (see figures 2 and 6).
In operation, the inductance current changes alternately between the values of IV and IP, as shown in Figure 6. When the system changes from cycle #1 inversion to cycle #2, the energy accumulated in the inductor is transmitted to the load, and the voltage of the energy storage capacitor increases with the transfer of energy to it.
Let k = R1 / (R1 + R2). When VO is greater than k * VREF, the internal comparator U1 turns over, and the output current drops to zero at time T1. Accordingly, the output capacitor contains all the energy previously stored in the inductor, and the output voltage keeps increasing above the reference value specified by parameter k * VREF. The final voltage vohp represents the amplitude of high-end ripple.
At this time, the output voltage begins to drop (because there is no more energy supplied from the inductance), and the comparator will flip when VO is less than k * VREF according to the time T2 determined by the load. The DC / DC converter continues to cycle #1 work, but the output voltage continues to drop, because it takes more time to reach the IP current value (time T3), and after the inductor is charged from zero, when it reaches the low VolP of ripple amplitude, the cycle #2 starts a new cycle. The waveform diagram of Fig. 6 describes this mechanism.
Conclusion of this paper
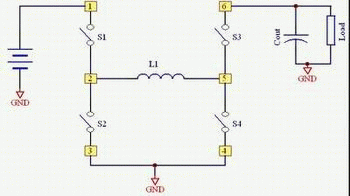
The operating voltage of the smart card has been upgraded to be suitable for any chip specifically for this application. The initial iso7816-3 and EMV (europay / Master Card / visa) documents now include 1.8V, 3.0V and 5.0V as applicable working power supply. Therefore, the physical interface between the card and must be able to adapt any of the above power supplies to the main MPU. The power supply must maintain the operating conditions specified in Table 1. In addition, the power supply must be able to operate at 750 μ Disconnect from the card within s, especially when the card is pulled out with power.
In addition to static operation, the power supply can keep the output voltage within the tolerance when the load is 100mA / 400ns pulse. Such requirements relate to the working state of the system, not just the power supply.
DC / DC converter
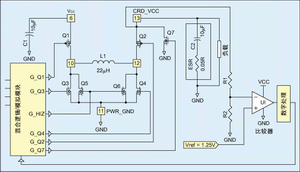
With the increasing application, from battery powered portable system to TV satellite receiver, smart card interface must deal with a large input voltage range and have high efficiency. Basically, it can be implemented in any type of structure as long as it can provide the required power for the card. For example, it can be designed as a switching capacitor based converter, but considering the portable POS system, its limited efficiency has become a key problem. For GSM applications, it is different. Because the output power is limited to 50MW, this capacitor based structure is preferred on the radiotelephone PCB to save space.
Considering that for the portable module of POS machine, energy saving is the key problem, so the structure based on inductance is given priority to improve the efficiency as much as possible. In fact, when the output power is up to 300MW, the efficiency of the inductor structure in the whole working voltage range can reach 85%, which is a level difficult to achieve by low-cost switched capacitor technology.
On the other hand, because the input voltage can be from 2.70v low to 5.50V high (after the battery is almost exhausted or after the battery is charged), the structure must automatically and without adjustment switch from boost to step-down, and vice versa. The concepts described in Figure 1 have been developed to meet these requirements and to maintain EMV as the main goal in the design.
The real system realized in silicon bare chip is more complex, because it can not have voltage spikes, but also realize adjustment and low ripple. It is important that the circuit meet all EMV specifications, especially the power down sequence, power off sequence and output short-circuit current.
To meet these requirements, the converter shown in Figure 2 adds several additional NMOS and PMOS transistors.
The system operates according to the concept of two cycles (see Figure 2 and figure 3 for all notes), and has a special structure considering the requirements of smart card:
Cycle 1: Q1 and Q4 are turned on, and inductor L1 is charged by external battery. At this stage, Q2 / Q3 and Q5 / Q6 are turned off.
The current flowing through Q1 and Q4 MOSFETs is internally monitored and turned off when it reaches the ipeak value (peak current, depending on the programmable output voltage value). At this point, cycle 1 is completed and cycle 2 begins. The "on" time is a function of the battery voltage and the inductance network values (L and Zr) connected between pins 10 and 11.
To prevent uncontrolled operation, 4 μ The s-pause structure ensures that the system operates only in a continuous cycle 1 loop under overload or low battery input.
Cycle 2: Q2 and Q3 are turned on, and the energy stored in inductor L1 is transferred to the external load through Q2. At this stage, Q1 / Q4 and Q5 / Q6 are turned off. The current flow cycle is a constant value of 900ns (typical value), if CRD_ If the VCC voltage is lower than the specified value, repeat cycle 1 after this period of time.
When the output voltage reaches the specified value (1.80v, 3.0V or 5.0V), Q2 and Q3 are shut off immediately to avoid Overvoltage on the output load. At the same time, two additional NMOS Q5 and Q6 are turned on to completely discharge the current stored in the inductor and avoid ringing and voltage spikes on the system. Figure 3 shows the theoretical waveform of DC / DC converter.
When CRD_ The VCC is programmed to 0V, or when the smart card is pulled out of the socket, the active pull-down Q7 quickly discharges the output energy storage capacitor to ensure that the output voltage is less than 0.40V when the card slides on the ISO contact. Due to the low on resistance of Q7, the output voltage is less than 100 μ It drops rapidly to 400mV within s, which is far lower than the maximum value of 750 specified by EMV μ s。
Output voltage ripple, although not directly specified by iso7816-3 or EMV, plays an important role in the operation of smart card. Its peak to peak value depends on the following two main electrical parameters:
1. Total series resistance between output silicon structure and net energy storage capacitor;
2. Voltage stabilization, that is, the ability to detect the output voltage with small threshold and lag.
The two parameters depend on the internal welding wire connecting the chip to the outside, the pin contact connecting the series resistance of the energy storage capacitor, and the printed copper wire used to connect the pin to the load. When a large current passes through the pin, the multi welding wiring technology is widely used to reduce the series resistance to 50m (, or if a wider welding wire is used, the resistance value is lower.
The width of printed circuit board routing can be determined according to the current processing needs of a given application. In addition, the series resistance can be a problem because the external passive components involved vary greatly with different applications. The key part is the energy storage capacitor, because (for economic reasons) it is generally a low-cost type, but this will produce high voltage spikes that can hardly be completely eliminated.
Depending on the type of technology used to develop capacitors, parasitic elements may have relatively high values and produce large uncontrollable spikes. As shown in Figure 4, this equivalent series resistance (ESR) is very easy to cause such spikes because the supply current flows directly through it and brings high-voltage pulses into the output source.
Based on the experiments carried out in the characterization of ncn6001 and ncn6004a, the best scheme is to use two parallel 4.7 μ F / 10V / ceramic / X7R capacitor to realize CRD_ VCC filtering. ESR does not exceed 50m? In the whole temperature range?, Moreover, the combination of standard components provides an acceptable tolerance of - 20% to + 20%, and the cost increase is limited. Table 2 gives a general comparison of common capacitor types. Figure 5 shows the CRDs observed on the ncn6001 or ncn6004a demo board for different capacitor types for output voltage filtering_ VCC ripple. The large and fast transients observed on the above curve are very difficult to filter out because of their high energy. Clearly, aluminum capacitors are not suitable for such applications and should be avoided.
The second parameter depends on the performance of the internal comparator, voltage reference tolerance and digital processing. The voltage reference is derived from a stable bandgap circuit with a tolerance of ± 3%. On the other hand, the deviation and drift of simulation function are reduced by high-end integration technology. Detailed analysis of DC / DC operation helps to understand the impact of each element on the output voltage ripple (see figures 2 and 6).
In operation, the inductance current changes alternately between the values of IV and IP, as shown in Figure 6. When the system changes from cycle #1 inversion to cycle #2, the energy accumulated in the inductor is transmitted to the load, and the voltage of the energy storage capacitor increases with the transfer of energy to it.
Let k = R1 / (R1 + R2). When VO is greater than k * VREF, the internal comparator U1 turns over, and the output current drops to zero at time T1. Accordingly, the output capacitor contains all the energy previously stored in the inductor, and the output voltage keeps increasing above the reference value specified by parameter k * VREF. The final voltage vohp represents the amplitude of high-end ripple.
At this time, the output voltage begins to drop (because there is no more energy supplied from the inductance), and the comparator will flip when VO is less than k * VREF according to the time T2 determined by the load. The DC / DC converter continues to cycle #1 work, but the output voltage continues to drop, because it takes more time to reach the IP current value (time T3), and after the inductor is charged from zero, when it reaches the low VolP of ripple amplitude, the cycle #2 starts a new cycle. The waveform diagram of Fig. 6 describes this mechanism.
Conclusion of this paper
Under working conditions, DC / DC converter with 85% efficiency is developed and applied to smart card power supply, which can meet all complex iso7816-3 specifications. The system has sufficient robustness to prevent system latch when the load changes rapidly from zero to peak, even when the battery is at any end of the input voltage range. In addition, short-circuit current protection avoids any thermal runaway, because the trigger point of overload current will decrease with the increase of temperature. This structure has passed EMV and EMV co procedures level 1 and level 2, including EMV2000 protocol.
Disclaimer: This article is transferred from other platforms and does not represent the views and positions of this site. If there is infringement or objection, please contact us to delete. thank you! |