Anba Aoku adaptive AI millimeter wave radar software and high energy efficiency CV3 AI domain controller master chip of 5 nm process realize centralized processing and pre fusion of original data of 4D imaging millimeter wave radar for the first time.
On December 6, 2022, in Santa Clara, California, the United States, Ambarella (hereinafter referred to as "Ambarella", NASDAQ stock code: AMBA, a semiconductor company focusing on AI visual perception chips) is today ahead of the industry‘s first centralized 4D imaging millimeter wave radar architecture, which can not only centralize the processing of raw millimeter wave radar data, but also input with other sensors, such as cameras, laser radars and ultrasound, Conduct in-depth low-level integration. This breakthrough architecture provides ADAS and L2+to L5 auto drive system as well as AI algorithm of intelligent robots with more advanced environmental awareness and safer path planning. Anba Aoku‘s unique millimeter wave radar technology uses AI algorithm to support the dynamic adaptation of radar waveform to surrounding scenes, and can output ultra dense point clouds with accuracy up to 0.5 degree angular resolution, tens of thousands of points per frame, and the effective working distance exceeds 500 meters. All the performance indicators are achieved by reducing the antenna MIMO channel by an order of magnitude, which not only reduces the data bandwidth, but also reduces the power consumption. Anba centralized 4D imaging millimeter wave radar equipped with Aoku technology has a more flexible sensing system and higher performance, helping system integrators take the lead in the design of the next generation radar.
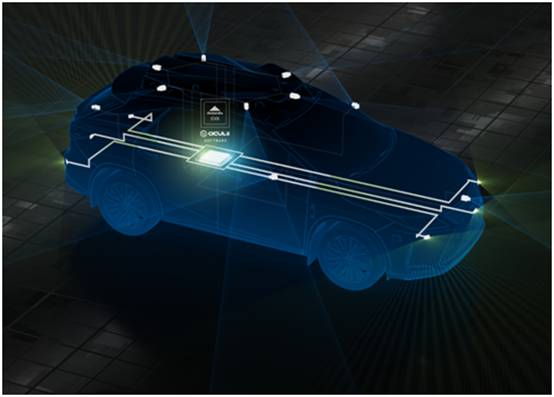
"In 2021, about 100 million millimeter wave radars will be produced in the automotive ADAS field in the global market." C é dric Malaquin, chief analyst of the RF equipment and technology team of Yole Intelligence, a global well-known market research and strategy consulting company, explained. "With the continuous improvement of regulatory requirements on vehicle safety and the gradual advancement of more advanced auto drive system, we expect that this number will increase 2.5 times by 2027". In fact, the OEM has evolved from the current configuration of 1-3 millimeter wave radars for each vehicle to at least 5 millimeter wave radars for each vehicle [1]. In addition, the industry has a tit for tat view on whether the millimeter wave radar should adopt distributed module processing or centralized processing, as well as how to do related development. One approach is to centralize the data of multiple radars, which will enable the OEMs to obtain higher performance imaging millimeter wave radar systems to achieve new ADAS/AD functions, and optimize the cost of millimeter wave radar modules.
This unique and cost-effective new architecture was finally implemented on the main chip of Anba CV3 AI domain controller. Anba optimized the algorithm and added a hardware unit specially designed for millimeter wave radar signal processing on the CV3 chip. CV3‘s AI performance advantage per watt has gradually been fully recognized by more customers in the industry. Its high computing performance and large memory capacity enable 4D millimeter wave radar algorithm to give full play to, resulting in radar perception results with high point cloud density, long detection range and high sensitivity. This allows autonomous vehicles and robots equipped with a single CV3 to efficiently focus on multi-sensor real-time processing perception, underlying fusion and path planning.
Wang Fengmin, President and CEO of Anba, said: "No other semiconductor and software companies in the industry have the leading full stack capabilities in millimeter wave radar algorithm, camera visual image processing, AI acceleration engine and other aspects at the same time. These professional capabilities enable us to create an unprecedented centralized domain control processing architecture. With the industry-leading performance power ratio of CV3, we can give full play to the leading advantages of Aoku millimeter wave radar algorithm and effectively achieve a new AI perception, sensor fusion and path planning, which will help us to dig out the full potential of ADAS, autopilot and robot markets in a deeper level. "
Due to the large amount of data, the 4D imaging millimeter wave radar technology of friends is difficult to effectively transmit and centralize. The high angular resolution required to provide 4D imaging millimeter wave radar requires thousands of MIMO antennas for each module, which will generate trillions of bits of data per second. At the same time, each radar module will consume more than 20 watts of power. A car needs at least six radar modules, and its data volume will be doubled. Therefore, it is extremely difficult to centrally process millimeter wave radar data on thousands of antennas.
The AI algorithm is used to dynamically control the existing MMIC equipment to modulate the radar waveform, and the AI algorithm is used to create a virtual antenna array. Aoku radar technology reduces the antenna array of each MMIC radar head in this new architecture to 6 transmit x 8 receive, and there is no need to connect the radar processor at the front end. As a result, the number of MMICs has been significantly reduced, while achieving extremely high 0.5 degree azimuth and pitch resolution. In addition, under the maximum duty cycle, the power consumption of the centralized architecture of Anba is significantly reduced, the bandwidth of data transmission is reduced by 6 times, and the edge radar processing is not required, thus avoiding information filtering and sensor information loss.
The centralized architecture with high cost performance and software definition can also dynamically allocate the processing resources of CV3 among different sensor types and among sensors of the same type according to the real-time situation. For example, in extreme rainy days, the effective data of remote cameras will decrease. CV3 can transfer some of its resources to enhance the data processing performance of millimeter wave radar. Similarly, if the vehicle is driving on the expressway in rainy days, CV3 can focus on the millimeter wave radar sensor data from the front to further expand the detection range of the vehicle and provide faster response. This adaptive optimization of the scene cannot be realized in the edge processing architecture, because in the edge processing architecture, millimeter wave radar data is distributed in each module for processing, and the processing performance is prepared for the worst case, so the performance of millimeter wave radar is often not fully utilized.
These two different millimeter wave radar processing methods are summarized in the following table:
Millimeter wave radar for edge processing of friends
|
Anba‘s Centralized Processing Millimeter Wave Radar
|
Continuous and repeated millimeter wave radar waveform without considering environmental conditions
|
Oculii™ AI software algorithm can dynamically adjust the millimeter wave radar waveform according to the surrounding environment
|
The module contains MMIC+edge radar processor
|
Only MMIC is included in "millimeter wave radar head"
|
Millimeter wave radar detection processing in millimeter wave radar module
|
Millimeter wave radar detection and processing in central processing unit
|
T bit millimeter wave radar data per second per module (too much to transmit and process in a centralized way)
|
Millimeter wave radar data transmission bandwidth is reduced by 6 times, thus facilitating centralized processing
|
1+to 2 degree angular resolution
|
0.5 degree azimuth and pitch resolution
|
High power consumption: Each millimeter wave radar module uses 1000 antenna MIMO channels
|
Low power consumption: antenna MIMO channel is one order of magnitude less (each MMIC millimeter wave radar head without processor has 6 transmitting x 8 receiving antennas)
|
Dynamic allocation of computing resources is not supported (considering the worst case)
|
Support dynamic allocation of CV3 processing resources between different sensors and sensors of the same type according to real-time conditions
|
Low performance of integrated radar processor
|
The built-in radar processor of CV3 is more than 100 times faster than the traditional edge millimeter wave radar processor (DSP)
|
CV3 marks the next generation CVflow of Anba ® The first appearance of the architecture includes neural network vector processor and general computing vector processor, both of which include special signal processing for millimeter wave radar. These processors can achieve high performance 100 times faster than traditional edge millimeter wave radar processors by working together and combining with Aoku‘s advanced radar sensing algorithm.
The advantages of the new centralized architecture also include that it is easier to upgrade OTA software, so as to continuously improve and adapt to new requirements in the future. In contrast, after determining the processor and operating system used by each module, the processor of each edge millimeter wave radar module must be updated separately; A single OTA update can be directly pushed to the CV3 master chip and summarized in all radar heads of the system. These radar heads only need radar transceiver chips instead of radar processors, which reduces the cost of front mounting and the cost of replacing materials after accidents (most millimeter wave radars are located behind the bumper of vehicles). Compared with the convenience of updating the software of the new generation centralized millimeter wave radar, many millimeter wave radar modules deployed today have never updated the software due to the complexity of traditional distributed radar updating software.
The target applications of the new centralized millimeter wave radar architecture include ADAS and L2+to L5 autonomous vehicle, as well as autonomous mobile robots (AMR) and automated guided vehicles (AGV) robots. These designs are simplified through the unified and flexible software development environment of Anba, which provides an upgradable software platform for automotive and robot developers. The performance range extends from ADAS and L2+to L5.
The latest centralized architecture will be displayed during 2023 CES, and this exhibition is only open to the invited guests of Anba. Contact your sales representative if necessary. For more samples and evaluation information about Aoku AI millimeter wave radar technology and CV3 AI domain controller main chip series, https://www.ChipSourceTek.com
About Anba
Anba‘s products are widely used in artificial intelligence computer vision, video image processing, video recording and other fields, including video security, advanced driver assistance system (ADAS), electronic rear-view mirror, tachograph, driver and cabin intelligent monitoring, intelligent car driverless driving and robot applications. Anba‘s high-performance, low-power AI processor provides ultra-high definition image processing, video compression and powerful neural network processing. It can extract valuable data from high-resolution video and radar information, and plays a major role in fields such as intelligent perception, sensor fusion and central domain control processing systems.
The latest centralized architecture will be displayed during 2023 CES, and this exhibition is only open to the invited guests of Anba. Contact your sales representative if necessary. For more samples and evaluation information about Aoku AI millimeter wave radar technology and CV3 AI domain controller main chip series, https://www.ChipSourceTek.com
Disclaimer: This article is transferred from other platforms and does not represent the views and positions of this site. If there is any infringement or objection, please contact us to delete it. thank you!
|