Ansomy launched ecoSpin series, redefining brushless DC motor control
Time:2022-11-13
Views:1530
ecoSpin ™ The brushless DC motor control scheme includes an embedded grid driver and a microcontroller engine, which can work reliably at a voltage of up to 600 V, and the power can be expanded
Ahead of smart power supply and smart sensing technology, Ansemi (NASDAQ: ON) launched a new ecoPin ™ BLDC series brushless DC (hereinafter referred to as "BLDC") motor controller. By integrating control and drive functions into a complete system level package (SiP), Ansenmey has simplified the development of high-voltage motor control systems for HVAC, refrigeration and robot applications.
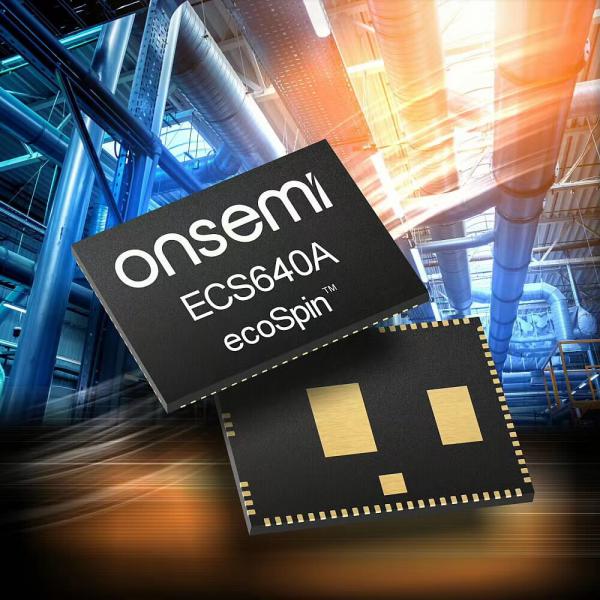
The first device in the ecoPin series is the ECS640A, a three-phase BLDC motor controller that can reliably operate under high voltage up to 600 V. Small size ECS640A with reliable grid driver, Arm ® Cortex-M0+microcontroller, three detection amplifiers, three boost diodes, and support sensorless or sensorless motor control architecture.
Michel De Mey, Vice President of Industrial Solutions Division of Ansomy, said, "The adoption of this highly integrated solution can shorten the time to market, because it eliminates the design cycle of applications and simplifies the reuse of the solution when it is required to expand the BLDC motor power level. This solution replaces many larger and more complex devices, which improves the reliability. At the same time, the PCB wiring area is reduced by about 20% compared with the discrete solution, making the overall solution small and compact."
This is integrated in a single IC package (10 × 13 mm), optimized power level layout and reduced noise, thus redefining the control performance of BLDC motor. By simply replacing discrete power devices and updating software, the scheme can be quickly reused on other platforms. The streamlining of bills of materials (BOMs) simplifies the challenges associated with purchasing many different discrete components.
To optimize performance, the ECS 640A supports traditional motor control technologies, including trapezoidal control and vector control. In addition, the internal Cortex M0 platform can also support more advanced direct flux and torque control algorithms. These technologies can improve the control of motor flux and torque in a wide speed range, and the power efficiency can be improved by 3% to 5%.
The ECS640A uses a compact system design and user-friendly tools to speed up the design process, bringing a new level of ease of use for BLDC motor control.
Disclaimer: This article is transferred from other platforms and does not represent the views and positions of this site. If there is any infringement or objection, please contact us to delete it. thank you! |