Operating principle of bootstrap circuit and selection of bootstrap resistance and capacitor
Time:2022-09-29
Views:1475
In some low-cost applications, especially for some 600V low-power IGBTs, the industry always tries to minimize the driver level cost. As a result, bootstrap power supply has become a widely used method to supply power to high-voltage grid drive (HVIC) circuits because of its simple circuit and low cost.
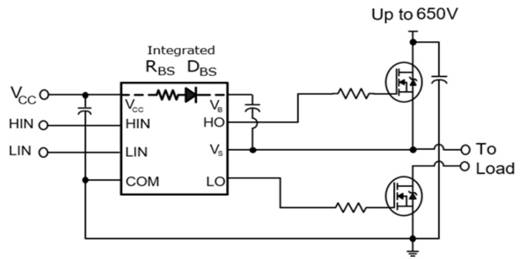
Operating principle of bootstrap circuit
As shown in the figure below, the bootstrap circuit only needs a 15~18V power supply to provide energy for the drive stage of the inverter. All the IGBTs at the bottom of the half bridge are directly connected to this power supply. The drivers of the IGBTs at the top of the half bridge are connected to the power supply Vb through the resistance Rboot and diode VF. Each driver has a capacitor Cboot to buffer the voltage;
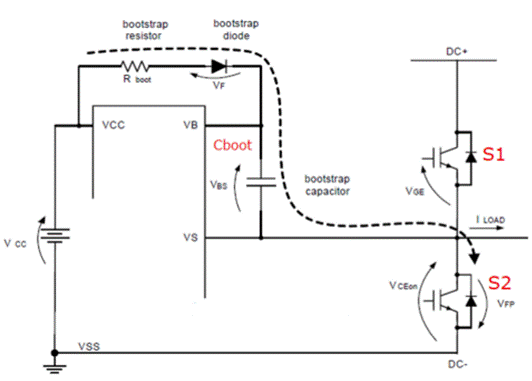
When the lower tube S2 is turned on and the Vs drops below the power supply voltage Vcc, Vcc charges the bootstrap capacitor Cboot through the bootstrap diode and the bootstrap resistor Rboot, generating Vbs suspension voltage at both ends of the bootstrap capacitor, and supporting the switch of HO to Vs. With the upper tube S1 switch, the bootstrap diode is in reverse bias when Vs is high voltage, and Vbs and power supply Vcc are separated.
Selection of bootstrap capacitor
The lower tube S2 is on, and the bootstrap capacitor (Cboot) is charged every time when the voltage of Vs is lower than the power supply voltage (Vcc). The bootstrap capacitor discharges only when the high-end switch S1 is on. The bootstrap capacitor supplies power to the high-end circuit (VBS). The first parameter to be considered is the maximum voltage drop of the bootstrap capacitor when the high-end switch is on. The maximum allowable voltage drop (Vbs) depends on the minimum gate drive voltage to be maintained. If VGSMIN has the minimum gate source voltage, the voltage drop of the capacitor must be:

Including:
Vcc=power supply voltage of driver chip;
VF=positive voltage drop of bootstrap diode;
Vrboot=voltage drop across the bootstrap resistor;
Vcessat=conduction voltage drop of lower tube S2
The bootstrap capacitance is calculated as:
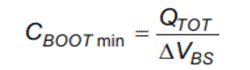
Including:
QTOT is the total charge of the capacitor.
The total charge of the bootstrap capacitor is calculated by Equation 4:

The following table is recommended for calculating bootstrap capacitance with IR2106+IKP15N65H5 (18A @ 125 ° C) as an example:
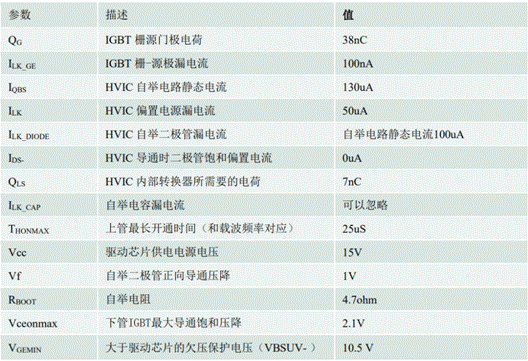

The recommended capacitance value must be selected according to the device used and the application conditions. If the capacitance is too small, the drop ripple of the bootstrap capacitor is too large when the upper tube is turned on, reducing the service life of the capacitor, increasing the switch tube loss, and reducing the switch reliability; If the capacitance value is too large, the charging time of the bootstrap capacitor will be reduced, and the low end conduction time may not be enough to make the capacitor reach the bootstrap voltage.
Select bootstrap resistance
The bootstrap resistor is mainly used to prevent current limiting when charging the bootstrap capacitor for the first time. The drive chip of Infineon has built-in bootstrap diodes and resistors, so it is unnecessary to consider the selection of resistors. This is just an analysis of the principle. When an external bootstrap resistor is used, the resistor RBOOT brings an additional voltage drop:
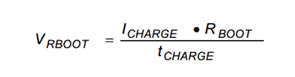
Including:
ICHARGE=charging current of bootstrap capacitor;
RBOOT=bootstrap resistance;
TCHARGE=charging time of bootstrap capacitor (conduction time of lower tube)
The resistance value (generally 5~15 Ω) should not be too large, otherwise the VBS time constant will increase. When calculating the maximum allowable voltage drop (VBOOT), the voltage drop of the bootstrap diode must be considered. If the voltage drop is too large or the circuit cannot provide enough charging time, we can use a fast recovery or ultra fast recovery diode.
In actual selection, we may consider the limitation that bootstrap resistance is too small:
1. Excessive charging current triggers sampling resistance overcurrent protection in small power output applications
2. Too small bootstrap resistance may cause higher dVbs/dt, which will result in higher Vs negative pressure. We will continue to discuss the harm of Vs negative pressure later.
3. Excessive charging current will easily lead to low Vcc voltage in the charging phase, resulting in undervoltage protection.
4. It is easy to cause overcurrent damage to the bootstrap diode.
As shown in the figure below, Infineon‘s new generation 2ED218xS06F/2ED218x4S06J high current series SOI technology half bridge drive internal circuit is integrated with bootstrap resistor and bootstrap diode, which can help customers avoid the design trouble of bootstrap resistor and diode circuit.
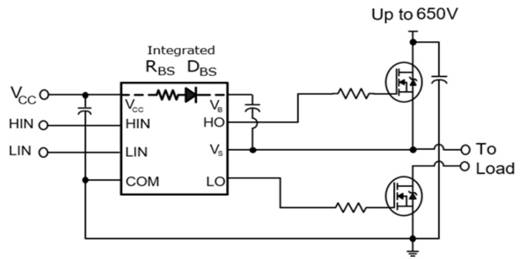
Key points of bootstrap circuit design
In order to ensure that the bootstrap circuit can work normally, you need to pay attention to many problems:
1. After starting work, always lead the lower bridge arm IGBT of the half bridge, so that the bootstrap capacitor can be recharged to the rated value of the power supply. Failure to do so may result in uncontrolled switch states and/or errors.
2. The capacity of the bootstrap capacitor Cboot must be large enough to meet the energy requirements of the upper bridge arm driver in a complete working cycle.
3. The voltage of bootstrap capacitor shall not be lower than the minimum value, otherwise undervoltage lockout protection will occur.
4. When the bootstrap capacitor is initially charged, a large peak current may appear. This may interfere with other circuits, so it is recommended to use a bootstrap resistor with low impedance for current limiting.
5. On the one hand, the bootstrap diode must be fast because its operating frequency is the same as that of IGBT. On the other hand, it must have a blocking voltage that is large enough, at least as large as that of IGBT. This means that 600V bootstrap diode must be selected for 600V IGBT.
6. When selecting the Vcc voltage of the drive power supply, the voltage drop inside the driver and the voltage drop of the bootstrap diode and the bootstrap resistor must be considered to prevent the IGBT grid voltage from being too low and causing increased turn-on loss. Furthermore, the determined voltage must subtract the saturation voltage drop of the lower tube IGBT, which causes the upper and lower tube IGBTs to open under different forward grid voltages. Therefore, Vcc should ensure that the upper tube has sufficient grid voltage and the lower tube grid voltage does not become too high.
7. It is uncommon to use bootstrap circuit to provide negative pressure. In this way, attention must be paid to the parasitic conduction of IGBT.
Finally, the bootstrap circuit also has some limitations. Some applications, such as motor driven motors, work at low speed and high current for a long time, and the opening duty cycle of the lower tube is always small, resulting in insufficient bootstrap charging of the upper tube. In this case, specific duty cycle compensation or independent power supply should be made in the PWM algorithm.
Disclaimer: This article is transferred from other platforms and does not represent the views and positions of this site. If there is any infringement or objection, please contact us to delete it. thank you! |