What kind of BLDC motor control chip is needed for humanoid robots
Time:2024-01-16
Views:360
Key content overview:
·BLDC motor control can use dedicated chips (ASSP) and general-purpose MCUs
·Sensorless BLDC motors are more common, with hardware based control algorithms
·Integration trend: integrating pre drivers, gate drivers, and power management
On December 13th, Musk released the next-generation humanoid robot prototype Optimus Gen 2, which is one step closer to mass production. China is also accelerating the development of humanoid robots. Recently, the Ministry of Industry and Information Technology issued the "Guiding Opinions on Innovative Development of Humanoid Robots", which pointed out that humanoid robots are expected to become disruptive products after computers, smartphones, and new energy vehicles, and clarified the goals and timeline for the development of humanoid robots.
At present, there are many local manufacturers in the middle reaches of China‘s humanoid robot industry chain, including Ubisoft, Data Technology, Xiaomi, Tencent, Fourier Intelligence, Xiaopeng Motors, Chasing Search, Yushu, Zhiyuan Robotics, etc. Among them, only Ubisoft has launched mass-produced products, but the cost is expensive. Upstream core component manufacturers include frameless torque motor manufacturer Buke Co., Ltd., hollow cup motor manufacturer Mingzhi Electric Appliance, reducer manufacturer Green Harmonic, Zhongli Dede, and Double Ring Drive, control system manufacturer Huichuan Technology, encoder and sensor manufacturer Haozhi Electromechanical, planetary roller screw manufacturer Changsheng Bearing, Qinchuan Machine Tool, etc. (Note: No frame indicates no casing for the motor; hollow cup indicates no iron core rotor for the motor)
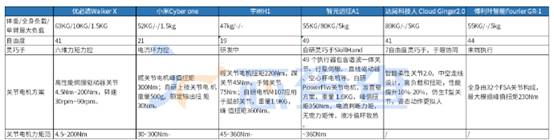
Figure caption: Comparison of joint motors of several major humanoid robots in China (incomplete statistics, core check table)
Frameless torque motor and hollow cup motor are key components of robot joints. Compared to these two types of motors, brushless DC motor (BLDC) is a more general and common type of motor. Some analyses suggest that the common humanoid robot joint motors belong to BLDC.
BLDC is not a new thing, it is almost everywhere, including household appliances, office equipment, electric tools, automotive electronic systems, etc., and emerging applications such as drones, electric vehicles, and the aforementioned robots are also inseparable from BLDC. Allied Market Research estimates that the global BLDC market size will increase from $33.2 billion in 2020 to $72.2 billion by 2030.
Figure caption: Growth of BLDC motors from 2020 to 2030 (Source: Allied Market Research)
The advantages of BLDC include high energy efficiency (usually up to 92%); Due to the absence of any brush friction, it can operate at higher speeds; More compact size, lower noise properties, better EMI curve, etc. But these advantages also come at a cost, as their control design is more complex. Below are several trends in the application of BLDC control chips.
Is it a dedicated chip or a general-purpose MCU?
BLDC motor control can use dedicated chips (ASSP) or general-purpose MCUs.
Specialized chips typically integrate hardware modules required for motor control, such as PWM controllers, current sensing, position sensing interfaces (usually Hall effect sensors or encoder interfaces), and protection circuits. Specialized chips typically have the advantages of high efficiency, low power consumption, and small size, and because they are specifically designed for motor control, they often provide excellent performance and stability.
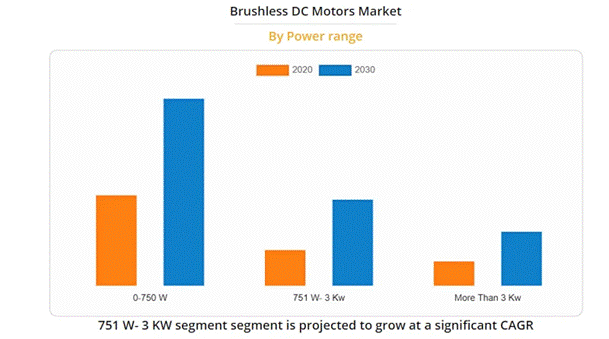
Image caption: BLDC motor control system (Image source: China Electric Port)
For BLDC motor control dedicated chips, suppliers usually provide a complete range of dedicated chip product combinations, such as ADI‘s analog-to-digital converters, amplifiers, embedded processors, iCouplers ® Digital isolators, power management devices, and real-time Ethernet solutions.
In the servo control system of motors, high-precision current and voltage detection can improve speed and torque control performance. In servo systems that use resistors for current sampling, the quality of the sampling signal is crucial to the electrical control performance. ADI provides a solution based on Σ-Δ A high-performance solution for modulators.
The performance of position detection is crucial for servo control, and optical encoders and rotary transformers are often used as position sensors. The conversion of servo control technology from analog to digital has driven the development of modern servo systems and also met the high requirements for the performance and efficiency of motor control.
From the perspective of prioritizing safety and protection, signal sampling and power device driving should adopt isolation technology. ADI‘s iCoupler digital isolator products can meet high-voltage safety isolation requirements.
Compared to specialized chips, BLDC motor control based on general-purpose MCU has its advantages - flexibility and programmability. MCUs typically contain one or more CPU cores as well as various peripheral interfaces and peripherals, and implement motor control algorithms through software programming. A 32-bit MCU has sufficient processing power to implement complex motor control algorithms, such as Field Oriented Control (FOC).
For example, the Microchip AVR EB series MCU can provide complex waveform control in BLDC motor systems, adjusting speed, timing, and waveform shape to create sine and trapezoidal waveforms; On chip peripherals can achieve multiple functions with minimal programming, quickly respond to changes in working conditions, and can be adjusted in real-time with almost zero latency. In addition, it can perform multiple tasks independently of the CPU, such as reading environmental sensors and serial communication, which can reduce the overall BOM cost.
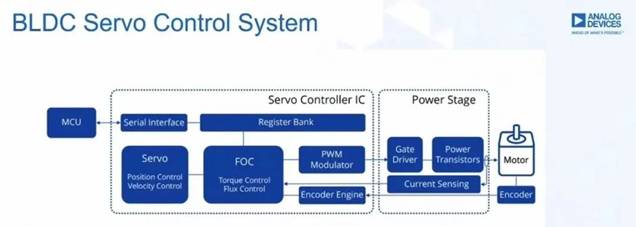
Image caption: MCU can provide complex waveform control in BLDC motor systems (Image source: Microchip)
Whether to choose a dedicated chip or a general-purpose MCU depends on the application requirements:
-If the application is cost sensitive and the motor control requirements are relatively simple, the dedicated chip ASSP may be a better choice due to its lower cost and higher integration.
-If the application requires higher flexibility, scalability, or complex task execution, then a general-purpose MCU may be more suitable. Although the initial development cost is high, the flexibility of MCU can adapt to future design changes and functional upgrades.
In practical applications, the design may combine specialized motor control chips and general-purpose MCUs, each performing its own duties. Specialized chips handle specific tasks of motor control, while MCUs are responsible for higher-level system control and communication functions. This hybrid solution can balance performance, cost, and flexibility.
Sensorless or more commonly, hardware based control algorithms
Sensorless BLDC motors may become more common, which requires monitoring and control of motor operation status through control algorithms.
From the perspective of performance and complexity, the development path of motor control algorithms has evolved from the initial 120 degree square wave control, to inductive SVPWM, gradually to inductive FOC, and finally to non inductive FOC control algorithms - control algorithms are becoming increasingly complex, and the development threshold is getting higher. In order to facilitate users to use the latest and optimal control solutions, it is an inevitable trend for motor control algorithms to reduce development thresholds through hardware implementation.
The early pure software algorithm development method for MCU was quickly replaced by intelligent integrated hardware, from square wave algorithm ASIC, sine like algorithm ASIC, integrated MDU, Cordic, etc., to a series of changes such as insensitivity FOC algorithm ASIC, realizing the evolution of motor control algorithm hardware.
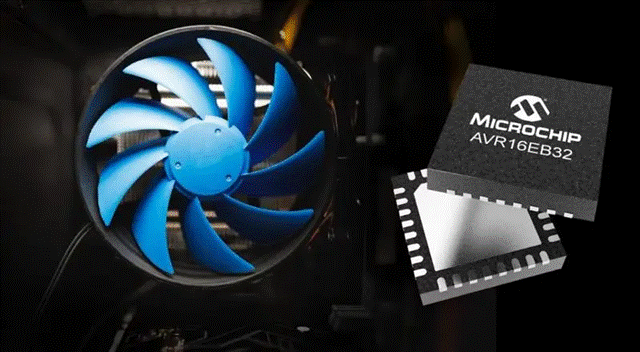
Image caption: Renesas MPU+Lattice FPGA dual chip architecture, supporting EtherCAT open architecture while implementing algorithm acceleration (Image source: China Electric Port)
In addition to ASICs, FPGAs are also used to implement FOC control algorithms. For example, China Electronics Port has partnered with globally renowned semiconductor solution suppliers Renesas Electronics and Lattice Semiconductor to launch a high-performance EtherCAT servo drive solution, using a Renesas MPU+Lattice FPGA dual chip architecture.
In this scheme, the current loop control is placed in the FPGA for hardware acceleration, greatly reducing delay, making the current loop faster and improving accuracy. FPGA has more advantages in achieving multi axis synchronous control, current loop control, PWM control, and output. In addition, FPGA can be flexibly matched with different models to achieve 1-6 axis motor control, which is more cost-effective. Renesas RZ/T1 MPU integrates EtherCAT hardcore controller internally, which has higher integration and better real-time control.
High integration is another trend in BLDC motor control chips, from complete separation to integrated operational amplifiers and comparators, integrated pre drivers, integrated power supplies and MOSFETs, and finally to fully integrated modules. In the design of humanoid robots, highly integrated chips help achieve miniaturization and lightweighting. Taking the Ansemy EcoSpin BLDC motor controller series as an example, the control and driver are integrated into one chip to simplify the development of high-voltage motor control systems in applications such as HVAC, refrigeration, and robotics. One of the products in this series, ECS640A, integrates six gate driver outputs to provide 350mA/650mA (typical value) gate current for external power devices, and Hall sensor inputs support sensor or sensorless operation.
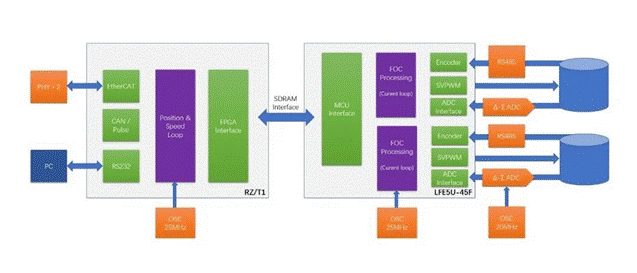
Image caption: BLDC motor control MCU integrated gate drive helps simplify humanoid robot design. Legend: Ansemy EcoSpin series products (Image source: Ansemy)
Summary
Humanoid robots are one of the hot applications in the current high-tech field. High precision motion control and attitude adjustment require the motors they use to have extremely high accuracy and dynamic response ability. At the same time, the system is required to handle control tasks of multiple motors to ensure coordination and synchronization. In addition, humanoid robots need to integrate a large number of electronic and mechanical components in limited space, such as motors and controllers. Overall, compared to traditional motors, BLDC motors are more suitable for the needs of humanoid robots mentioned above, which will inevitably drive the development of BLDC motor control chips. This article summarizes the products and solutions of such chips and their applications.
Disclaimer: This article is transferred from other platforms and does not represent the views and positions of this site. If there is any infringement or objection, please contact us to delete it. thank you! |