New Trends in Brushless DC Motor Drivers
Time:2023-10-18
Views:612
Brushless DC (BLDC) motors have been rapidly adopted in the market and a wide range of motion control applications, as they have significant advantages compared to traditional brushless DC motors. Less maintenance, higher operating speed, compactness, less electrical noise, and better torque to weight ratio, to name just a few. Despite these advantages, the cost of BLDC motors is higher than that of traditional DC motors because they require motor drive controllers (for electronic commutation) and rotor position sensors.
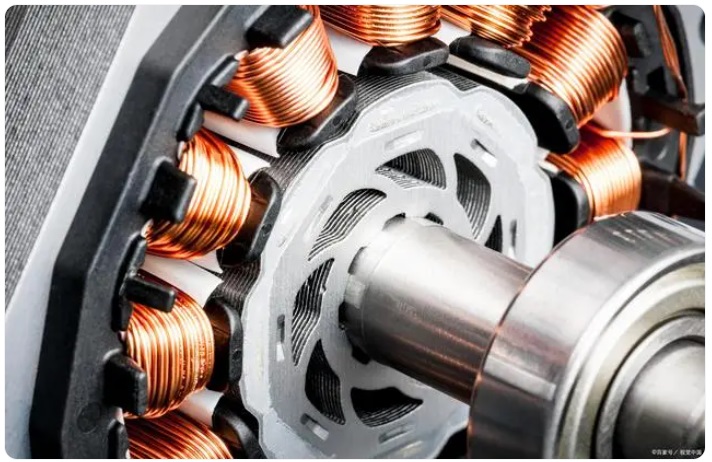
Sensorless control
Sensorless control technology is considered a cost saving benefit, which can also improve system reliability, reduce the number of electrical connections, eliminate mechanical alignment issues, and reduce motor size and weight. Generally speaking, the definition of sensorless control is to operate a BLDC motor without the commonly required rotor position sensor, eliminate rotor position sensors (such as optical encoders, Hall effect sensors, rotary transformers, cables, and decoding circuits), reduce manufacturing costs, improve reliability and durability.
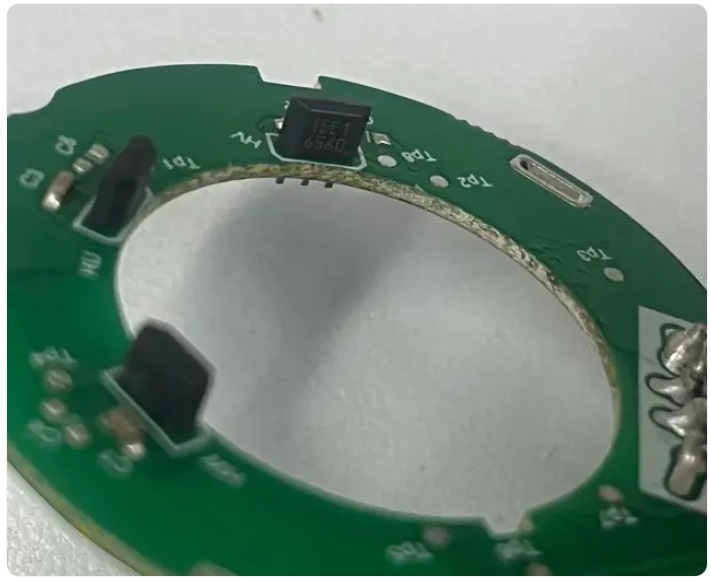
The BLDC motor driver with sensors uses a 3-phase PWM inverter with a rotor position sensor to perform commutation and/or current control. However, the methods for obtaining rotor position information are different. In sensorless control technology, rotor position information is determined by indirectly sensing the back electromotive force (electromotive force) of one of the three motor terminal voltages. Due to the fact that only two of the three BLDC motor phase windings are conducting simultaneously, the third non-conductive phase can indirectly calculate the back electromotive force of the rotor position and speed. At present, sensorless technology has not been widely adopted, and in the future, it is expected to become the main BLDC motor control method.
Reduced torque ripple
Although BLDC motors have many advantages, they have a limiting factor: they tend to exhibit torque pulsation. These pulsations can cause acoustic noise and vibration, and seriously limit the performance of the system, especially in high-precision and high stability applications. In high-speed applications, torque ripple can be filtered out through the inertia of the load. However, at low speeds, when they are most pronounced, torque ripple greatly limits performance. Torque ripple is caused by the design of BLDC motors and PWM drive controllers, including geometric defects in the motor, inaccurate commutation, fidelity of current drive waveforms, phase delay, friction, and hysteresis in the motor. They can be reduced by better motor design or the use of better drive controllers.
Torque ripple can be divided into two categories: cogging torque and commutation torque. cogging torque is generated by the magnetic resistance change caused by the stator slot opening during rotor rotation. The cogging torque can be reduced by changing the motor design, such as tilting the stator slots, selecting fractional slot/pole motor designs, or selecting magnet widths relative to slot spacing. The commutation torque ripple is generated by the PWM inverter of the driver and is due to current hysteresis or high-frequency current ripple generated by the inverter. During commutation, one phase is disconnected and the other phase is connected, so the rate of rise and fall of current in each phase is not equal. Therefore, the torque generated by the two-phase current during commutation will not be instantly added to the torque value. A fully excited phase will allow for smooth torque to be obtained within the commutation interval.
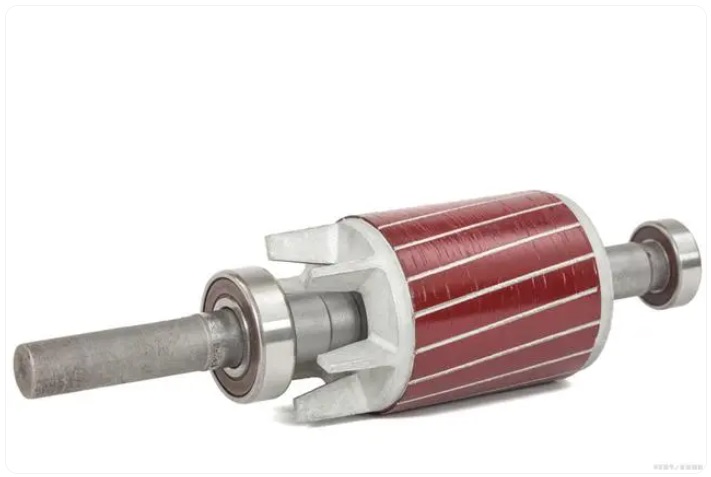
In order to minimize commutation torque ripple to the maximum extent, it is necessary to improve the BLDC driver. Several methods have been used in motor drive design to minimize commutation torque ripple. One method is to add an inductor capacitor (L-C) filter to reduce the high-frequency component of the inverter output to the motor. But a key factor in reducing torque ripple is to eliminate torque harmonics by adjusting the conduction phase of the winding to compensate appropriately. Four other methods have been introduced to reduce torque ripple: (1) using direct torque control, (2) dynamically changing input voltage, (3) adding torque estimation circuits, and (4) using artificial neural networks and active disturbance rejection control.
Integrated BLDC motor and driver
Integrated BLDC motors and drives are one of the latest trends, with the potential to reduce costs, improve reliability, and be compact. In the future, integrated BLDC motor drivers are expected to become market standards. In 2021, integrated BLDC motors increased by 47.7% and are rapidly replacing AC servo motors. More and more brushless DC integrated motors are accompanied by advanced feedback results. In addition, from 2019 to 2020, the compound annual growth rate of integrated BLDC motors with position control function is expected to reach 18.6%.
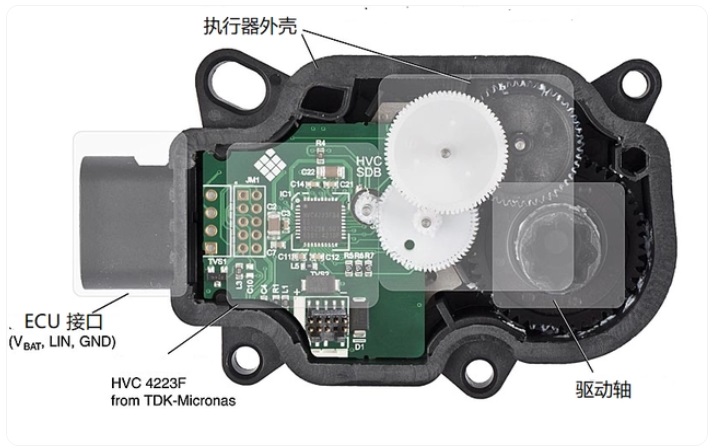
The integration of motors and driving electronic devices is the result of two new developments: (1) the continuous improvement of electronic component efficiency, leading to a reduction in the size of power electronic devices; (2) The rare earth permanent magnet of BLDC motor eliminates the heat source of the rotor, so the internal temperature rise is smaller than that of traditional DC motors, and the inverter control can be installed in the motor. Currently, the power range of integrated BLDC motors and drivers is within 100 watts. As the integrated BLDC motor market and size range increase, they will design simpler motor drive devices and eliminate the need for inverter control rooms, ventilation equipment, and cables between motors and inverters.
Digital Signal Processor
Most of the new trends in BLDC motor drives require high-performance controllers with high-speed microprocessors and high-density programmable logic controller technology. These high-performance controllers, known as digital signal processors, are rapidly being adopted in the market, driving their prices to steadily decline. Even low-cost digital signal processors can execute complex algorithms to improve motor performance in areas such as noise control, variable speed, and energy efficiency. In the past, basic digital controllers with 8-bit microcontrollers had sufficient bandwidth to achieve basic speed control.
As the complexity of motor control algorithms has increased, the demand for higher performance and more programmable solutions is also increasing, and digital signal processors provide most of the bandwidth and programmability required for such applications. Specifically, the bandwidth usage of low-cost digital signal processors achieves the following characteristics: 1. Proportional Integral Differential (PID) control to improve accuracy, 2. Sensorless algorithms to eliminate expensive speed and current sensors, 3. Random Pulse Width Modulation (PWM) to reduce noise and input filter size, 4. Ripple compensation algorithms to reduce the size of DC bus capacitors in the driver, 5 Power Factor Correction (PFC) to eliminate dedicated PFC controllers. Perhaps the biggest long-term benefits of digital signal processors are standardization of driver interfaces, complete digitization of drive systems, and easier means of "data transmission" with upper and remote control systems, making it easier to monitor and diagnose system faults.
conclusion
The design of BLDC motor drivers not only overcomes cost issues, but also provides motor driver performance that traditional DC motors cannot achieve. Implementing sensorless motor drivers that do not require rotor position feedback sensors is one of the latest trends in BLDC motor driver design, which can save costs. The change in PWM switching strategy within the motor driver is expected to eliminate issues related to torque ripple. Another major trend in BLDC motor drive technology is to integrate BLDC motors and drive electronic devices into a single package to simplify the system, minimize interconnect cables, reduce noise, and address motor drive compatibility issues.
Disclaimer: This article is transferred from other platforms and does not represent the views and positions of this site. If there is any infringement or objection, please contact us to delete it. thank you! |