BLDC motors are becoming increasingly popular, and integrated control solutions will be the future trend
Time:2023-04-11
Views:1101
In recent years, we have seen a clear trend, which is that BLDC (Brushless DC)/PMSM (Permanent Magnet Synchronous) motors have been increasingly used in various applications such as industry, automobiles, home appliances, electric tools, medical equipment, etc. This is because BLDC motors can operate at high speeds, typically exceeding 10000rpm or even 100000rpm, and have low rotor inertia, allowing for rapid acceleration, deceleration, and reverse rotation. They also have high power density, making the size of the motor more compact. Therefore, more and more application scenarios are adopting BLDC motors.
PMSM and BLDC with wound stator and permanent magnet rotor have similar structure, but the stator structure and winding are more similar to AC induction motor, generating sinusoidal flux density in the air gap. PMSM operates synchronously with the applied three-phase AC voltage and has a higher power density than AC induction motors, as there is no stator power used to induce the magnetic field in the rotor. The current design is also more powerful, allowing PMSM motors to have lower mass and moment of inertia simultaneously. Therefore, it is increasingly favored in many industrial driving, traction applications, and electrical appliance application scenarios.
The main driving factors for the popularity of BLDC/PMSM motors
Energy efficiency is one of the important indicators of electric motors, and industry standards related to energy efficiency are becoming increasingly strict. For example, since June 1, 2021, the new national standard GB18163-2020 implemented in China has stipulated that motors with an IE3 energy efficiency level or below have been prohibited from production and sales. Higher energy efficiency requirements have led to an increase in demand for semiconductor devices (including power devices and motor controllers), as the market is more inclined to adopt efficient motor solutions such as BLDC/PMSM, while also driving continuous innovation in motor control algorithms and power devices by semiconductor manufacturers.
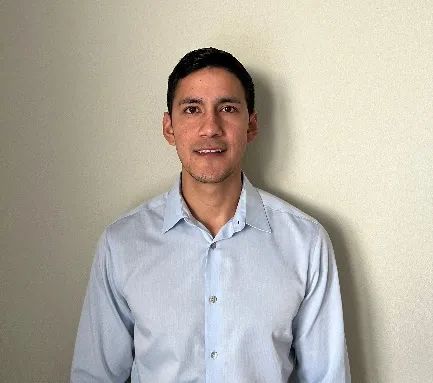
Image: Charlie Munoz, Application Marketing Manager, TI Brushless DC Motor Driver Product Line
In the opinion of Charlie Munoz, Marketing Manager for TI‘s Brushless DC Motor Drive Product Line, these new standards will encourage more customers to adopt new technologies to meet their efficiency, size, and cost requirements. Motor efficiency is an important issue in energy conservation, and motor power consumption accounts for a significant proportion of the overall energy consumption of electrical appliances and other applications.
Building a BLDC/PMSM motor system requires the joint efforts of motor suppliers and semiconductor manufacturers. For motor suppliers, the assembly cost of mechanical motors is too high to achieve additional efficiency, so they need semiconductor manufacturers to help improve the efficiency of motor drivers and algorithms to optimize the system.
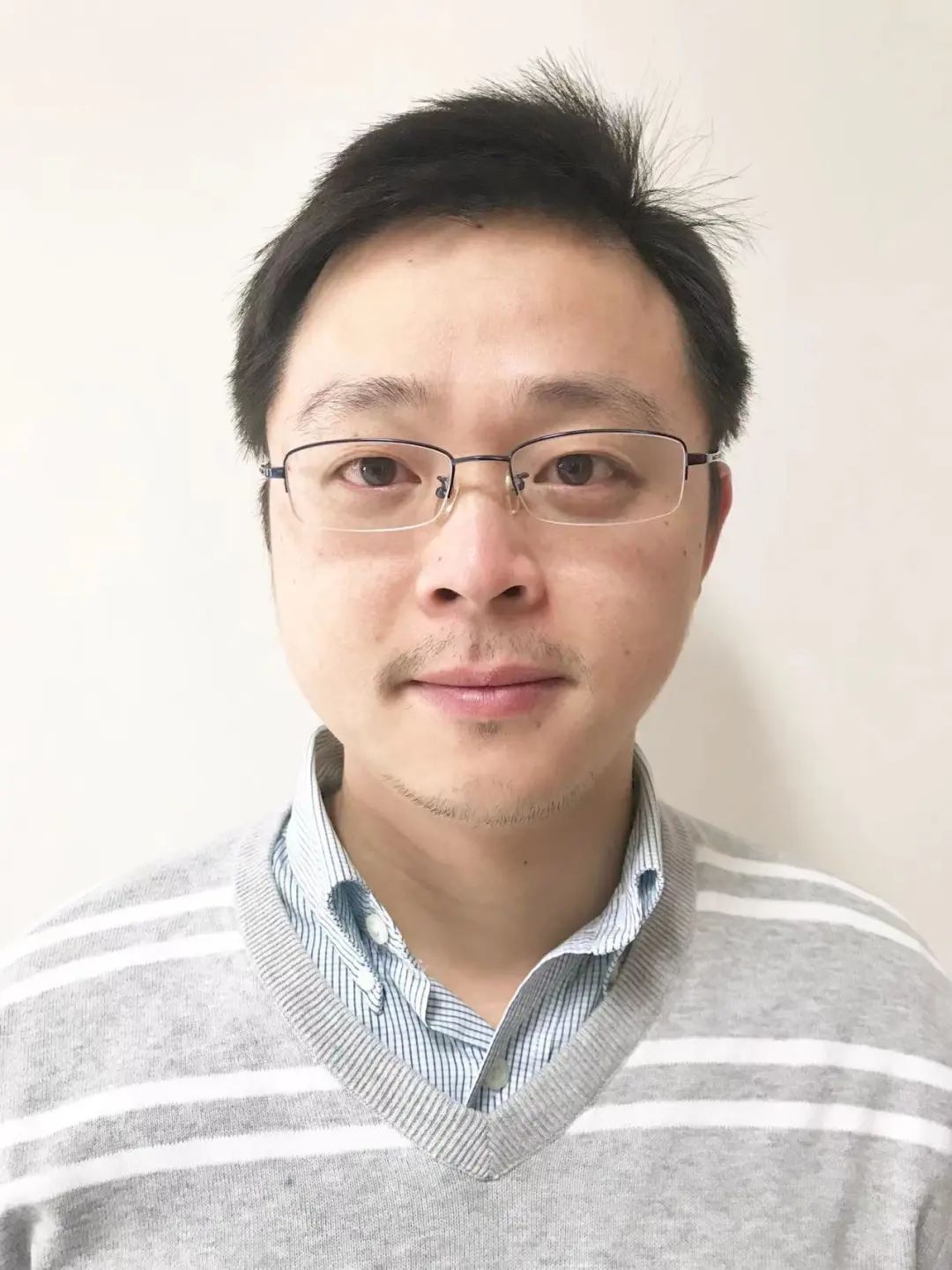
Figure: Zhu Zhen, Market Manager of the Industrial Automation Industry in ADI China
Zhu Zhen, Market Manager of the Industrial Automation Industry in ADI China, believes that BLDC/PMSM motors are gradually becoming the mainstream motor type. Due to the sharp decrease in the cost of controlling electronic equipment and the surge in new control algorithms, they are becoming increasingly popular in industries and home appliances.
Mark Gill, Vice President of Strategy and Marketing of Allegro MicroSystems, also saw this trend
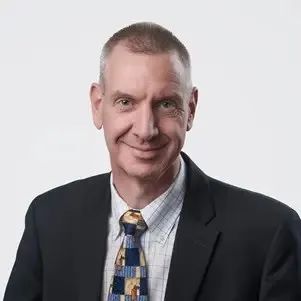
Image: Mark Gill, Vice President of Strategy and Marketing, Allegro MicroSystems
Taking home appliance applications as an example, Chen Ziying, Marketing Director of the Industrial Power Control Division of Infineon Technology, cited data from Omdia, stating that it is expected that by 2024, the frequency of household air conditioners will reach 99%, and the frequency conversion rates of washing machines and refrigerators will also increase year by year, reaching 94% and 75% respectively by 2024.
In addition to characteristics such as efficiency, reliability, and robustness, there is another reason why more and more application scenarios tend to use BLDC motors, which is noise. For example, some motor applications in the cockpit of electric/hybrid vehicles are sensitive to noise, and high-end models are increasingly inclined to use BLDC motors.
TI‘s Charlie Munoz told Electronics enthusiast website that another area that needs to pay attention to noise is household appliances, such as pumps and fans in dishwashers and refrigerators. In these applications, BLDC/PMSM motors and efficient drive systems are crucial for the success of the product.
Of course, BLDC motors can also be used in home fans, washing machine pumps, notebook computer fan, automotive ADAS, seat cooling and ventilation, EPS and braking, ventilators, server cooling fans and pumps and other application scenarios.
BLDC/PMSM Motor Drive Method and Selection Techniques
At present, there are various control solutions for BLDC/PMSM motors. According to Tristan Scott, Product Marketing Manager of Ansemy Motor Control Solutions, from the perspective of device integration, there are discrete power transistors, integrated modules, independent drive solutions without MCU participation, and SoC solutions that fully integrate controllers, drivers, and power transistors, which are suitable for different application scenarios; From a control perspective, the control solutions for BLDC/PMSM motors include trapezoidal algorithms with and without sensors, sinusoidal and magnetic field orientation. Sensor-based solutions benefit from low cost and easy commutation, while sensorless solutions can save circuit board space and improve system stability by eliminating the risk of sensor failures.
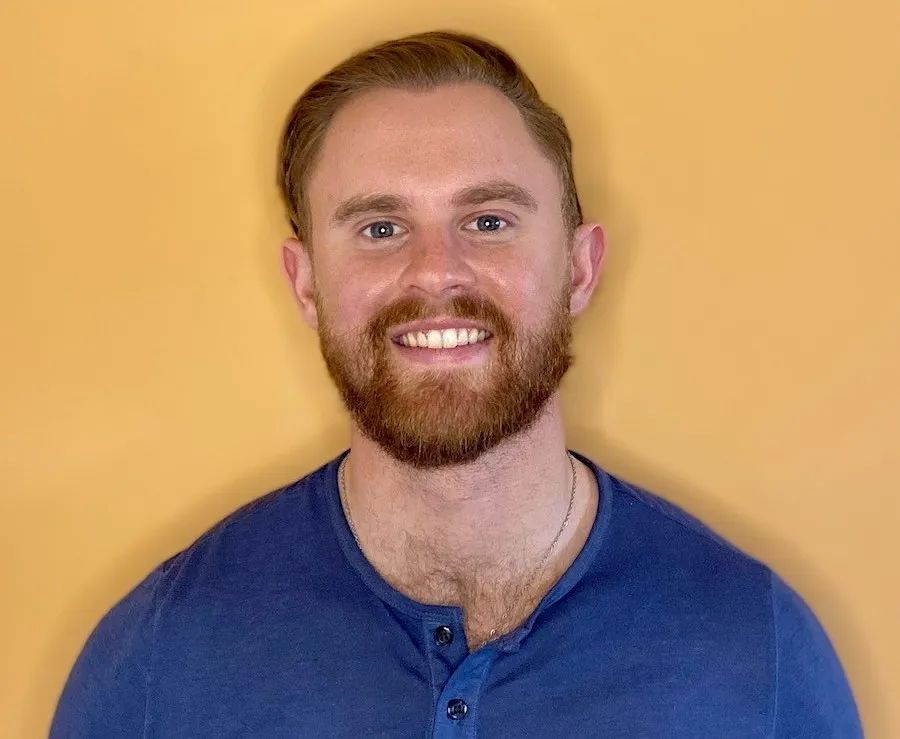
Tristan Scott, Product Marketing Manager, Ansemy Motor Control Solutions
Specifically, different solutions can be selected based on different system speed, torque, and position requirements. Charlie Munoz of TI pointed out that the trapezoidal algorithm is a low-cost and easy to implement control algorithm that requires low processing power, but has larger torque ripple compared to sinusoidal and magnetic field oriented control. Sine is an efficient and ultra silent solution, but it is more complex than trapezoidal algorithm and prone to higher switching losses. Finally, Field Oriented Control (FOC) has higher torque and motor efficiency, as well as lower noise and torque ripple compared to other commutation methods.
Ansemy‘s Tristan Scott believes that sine wave control and FOC have more application scenarios, and traditional trapezoidal wave control is gradually being replaced in some scenarios with high efficiency and low torque ripple requirements.
In terms of specific products, some manufacturers provide discrete hardware solutions, while others provide integrated solutions. For example, in terms of power devices, Ansemy can provide discrete IGBTs, MOSFETs, and SiC MoSFETs for use in medium to low power scenarios. At the same time, there are also IPM modules (integrated with power transistors and drivers) for use in medium to high power scenarios. IPM modules can help customers save PCB area, optimize heat dissipation and EMI performance, and shorten development time. In terms of control, they will provide a series of 3-phase drive and fully integrated (MCU+drive+power transistor) SoC solutions. In many scenarios, fully integrated solutions can effectively reduce the overall size of the motor and simplify the difficulty of customer development.
TI‘s BLDC products include discrete gate drivers and integrated gate drivers. The integrated gate driver controls the FET driver and the easy to operate gate driver, allowing customers to adjust the motor within ten minutes. Its main advantages are quiet and smooth motion control, orderly integrated system, high efficiency, high power density, expandable power supply and packaging, and very reliable. In this field, TI has some new products, such as MCF8315A and MCT8329A, for engineers to choose from.
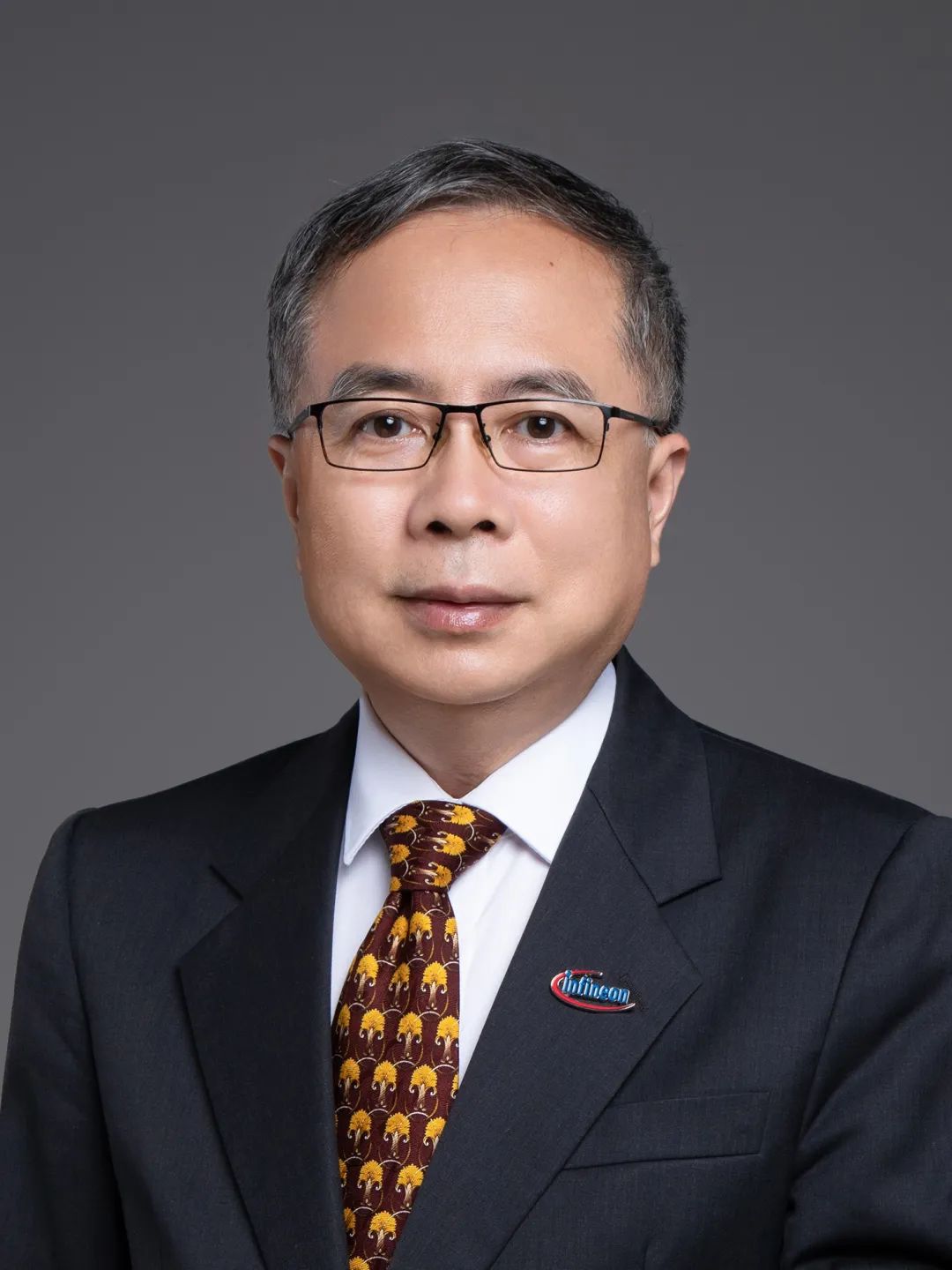
Image: Chen Ziying, Marketing Director of Infineon Technology‘s Industrial Power Control Business Unit
Infineon‘s motor drive solutions cover various applications ranging from tens of watts to tens of megawatts. Power semiconductor products include IGBT, SiC MOSFET, MOSFET, IPM intelligent power module, high-voltage high current thyristor, as well as motor drive chip iMOTION and MCU products for motor control applications. Among them, the iMOTION series products use DC bus current detection or bridge arm current detection, integrating all the control and analog interface functions required for sensorless field oriented control (FOC). It is a specialized motor driver chip that utilizes the system level knowledge accumulated by Infineon for a long time. It can complete single resistance sampling, sensorless dual motor control, and PFC control on a single chip. Customers do not need to program motor control, development is simple, and the research and development cycle is short. Mainly used in various motor drives mainly for variable frequency household appliances, with control objects including compressors, fans, water pumps, and general motors.
Allegro mainly provides ASIL safety level motor drivers, advanced motion control without code, and highly integrated small package motor controller solutions. Typical examples are A89332-1 and A89331, which help reduce system costs through three-phase sensorless fan controllers. The A89332 gate driver has a power outage braking (PLB) function, which can reduce energy consumption by stopping the rotation of fans that are powered off or unable to function properly. The A89331 three-phase motor driver with integrated MOSFET provides sensorless control, eliminating the need for Hall sensors in server cooling fan applications. A89331 adopts a sensorless sinusoidal driver to minimize the vibration of high-speed fans.
ADI can provide power electronic devices, isolation devices, current detection, position detection, vibration detection and other sensors, and motion controller and other devices. For example, high-voltage systems (>100 V) use insulated gate drivers to drive power semiconductors. And ADuM4122 is a single gate insulated gate driver that provides 3 A short circuit (<3 Ω), supports functional or enhanced insulation (up to~800 V DC bus), and provides swing rate control to achieve EMI/power loss optimization; It also supports high common mode transient suppression (CMTI) and low propagation delay for use with SiC and GaN power semiconductors. The ADuM160N multi-channel digital isolator can be used to isolate PWM signals and is used in conjunction with integrated power modules (IPM) that integrate gate drivers and power semiconductors. The ADuM6028 isolated power device can be used with digital isolators, isolated transceivers, and isolated data converters, providing a very compact 8-pin solution that is fully certified for safety and can be used instantly.
For low-voltage systems (<100 V), a 100 V half bridge driver LTC7060 that provides floating grounding and programmable dead time, or a 150 V protected high-end NMOS static switch driver LTC7000 that utilizes PassThru technology and adaptive breakdown protection, can be used to drive low-voltage semiconductors. The LTC7000 also supports programmable dead time (for optimizing efficiency), enhanced current control, and swing rate control (for reducing EMI).
ADA4570 and ADA4571 integrate AMR angle sensors and integrated signal regulators to provide higher precision absolute position detection (error<0.1 °, lifespan/temperature<0.5 °) for motor driver and server applications. They can operate reliably in harsh magnetic environments, support wide air gap tolerances without reducing angular error accuracy (unlike Hall/GMR/TMR), and simplify system design considerations.
So how do we choose the appropriate solution for motor control applications? Daniel Torres, director of motor business product line of Allegro MicroSystems, suggested that we should first understand the key factors of motor drive design: cost, size, reliability, robustness and time to market. The Allegro website can provide product selection tools based on common parameters.
The next decision may be to determine whether external microprocessors (called direct control) or products with integrated microprocessors (called intelligent control) are needed, each of which has two power level options. Firstly, there is an integrated pre driver, which uses an external high power gate driver; Secondly, it is a fully integrated full gate driver, typically suitable for low-power systems.
Overall, if Allegro‘s codeless Quiet Motion motor driver can meet the power/voltage requirements of the system, it is almost the best solution that can always meet the system‘s cost and time to market requirements. Allegro‘s solutions can provide high performance without the need for external microprocessors or software development.
For safety critical systems, Allegro can provide a series of brushless DC motor drives that meet the requirements of Automotive Safety Integrity Level D (ASIL D), which can meet the most stringent automotive application requirements.
Chen Ziying from Infineon suggested from the perspective of semiconductor companies that engineers need to develop products that are easy to get started with. Infineon has over 40 CiPOS and iMOTION solutions on its official website, and can provide more than 250 motor drive reference designs and related evaluation boards as references. When there is a need, you can log in to the Infineon Developer Forum, where you can also provide design support and technical exchange for motor drives.
Zhu Hua, Market Manager of the Security Interconnection Systems Business Unit of Infineon Technology, added that Infineon has mature MCU, power devices, sensor and sensorless motor algorithms, software, and hardware reference designs, which can provide customers with complete turnkey solutions and help them quickly develop mass-produced products.
TI provides four different steps to simplify the selection process in order to make the selection of BLDC products easier. Each step needs to be selected based on power level, architecture, motor control type, interface, and integration requirements. TI‘s brushless DC motor driver precautions and selection guidelines provide reference suggestions for selecting the best brushless DC solution for the system. The TI official website provides simple selection tools, such as parameter search, combination visualization, and simple use case content around characteristic applications, to help customers easily choose the right device.
New Technologies and Future Trends in Motor Control
With the development of BLDC/PMSM motor control technology, many new products and technologies have emerged, such as high voltage, sensorless control, sinusoidal and directional control, and sports health monitoring. Different companies also have different coping strategies.
According to Charlie Munoz of TI, TI quickly adapts to power demand by developing innovative integrated control solutions such as motor parameter extraction tools. Due to the complexity of BLDC motor design, smooth integration and driving of software algorithms and hardware components are required. TI is taking proactive measures to help quickly evaluate and adjust motors for maximum efficiency by providing a one-stop solution, code free integrated sensorless control drivers, adjustment guides, and GUI platform, thereby reducing design time and workload. We also provide application specific designs that can reduce noise by 2-3dB through techniques such as dead zone compensation and PWM modulation, "he pointed out.
ADI has expressed their views on the trend of motor control in the field of intelligent manufacturing, and they believe that to achieve the next generation of intelligent motion control solutions for intelligent manufacturing, multiple technologies need to be combined. When combined, these technologies can provide reliable and precise motion control for demanding industrial deployments, and access system information from advanced detection. This requires a combination of precise measurement, isolation and interface, industrial Ethernet, magnetic sensing, power management, machine health, and other technologies. For example, in order to support next-generation drives and motors that achieve complex motion control, digital isolation technology is needed to provide isolation data and isolation communication interfaces, such as RS-485, USB, and LVDS. Insulated gate drivers are also needed to drive high-end and low-end power semiconductors to provide reliable, safe, and highly reliable assets. The gate driver converts the logic level PWM signal into a high-end reference signal for controlling the power transistor. High voltage inverter applications typically use IGBT, but in the future, there will be a tendency to use SiC and GaN to increase switching frequency and/or reduce switching losses.
Infineon has utilized its professional manufacturing knowledge and long-term experience to develop a SiC groove process that avoids the reliability issue of gate oxygen in planar grids. Considering the requirement of motor drive for short circuit tolerance of power switches, Infineon‘s chips have a short circuit capability of 2-3 microseconds. The product is packaged in industrial standard TO247 packaging and SMT packaging TO267-7 packaging. Infineon also offers SiC MOSFET three-phase bridge power modules in Easy 1B and Easy 2B packages, which have low parasitic parameters and high power density. In addition to overall higher efficiency and lower losses, the higher switching frequency achieved by SiC technology directly benefits external and integrated servo drivers in more dynamic control environments. Under constantly changing motor load conditions, faster motor current response speed makes it possible.
Ansemy has also developed a TMPIM module based on SiC MOS for frequency converter applications, which can reduce the volume of inductance coils and improve thermal performance. Combined with its DTFC algorithm, this is the industry‘s first advanced motor control solution implemented on the M0+platform, providing engineers with more options.
When it comes to future development trends, integrated solutions are generally favored by everyone. Due to the fierce competition that will inevitably drive more innovation, integrated solutions can help customers reduce system volume, improve reliability, and reduce development cycles. Therefore, this development trend is more favored by the industry.
Daniel Torres, Director of the Motor Business Product Line at Allegro MicroSystems, explained that a future trend is to achieve integration of motor drive solutions at the highest level, with the benefits of smaller PCBs, smaller motors, and cost optimized designs. Through functional integration, the number of ICs required in the system can be reduced, which can reduce the system‘s demand for various resources, reduce current consumption, and directly improve system efficiency.
He also pointed out that improving integration can reduce the demand for other components and further reduce the bill of materials (BOM), which can provide customers with more flexibility. Improving integration can also shorten product time to market by simplifying design. In Allegro‘s motor driver, high integration eliminates the verification and corner analysis required for implementation in the system, thus achieving further optimization of the system.
Daniel Torres believes that future innovations may further reduce system BOM by integrating the functions typically present in microprocessors, allowing customers to ultimately remove microprocessors from the system.
Manufacturers that provide microprocessors are beginning to integrate more and more analog and power devices into their microprocessor products, and some have also solidified algorithms into their products, making customer development simpler and BOM costs lower.
epilogue
The motor control industry is shifting towards systems with higher efficiency, lower noise, and higher robustness. This transformation will allow more customers to transition to BLDC/PMSM motor systems. With the popularization of intelligent manufacturing and the rise of Industry 4.0, motors play a core role in power output, and the requirements for motor control are also increasing. Especially in the precision manufacturing industry, how to have excellent motion control capabilities will become a hot topic in the motor industry. Specific solutions require the support of various chips and solutions such as low drift, high precision, and high transient. In addition, durability/reliability/safety will also be increasingly valued, especially with the rapid increase in the number of motors, rapid maintenance becomes increasingly important. And all of these require strong support from chip manufacturers.
When it comes to future applications, as the industrial and automotive markets continue to show more electrification trends, BLDC/PMSM may see growth, and there may be more development in the industrial electrical market, such as vacuum cleaners, pumps, and fans, which are sensitive to noise in household environments. In addition, the BLDC/PMSM automotive market may have more applications in hybrid/electric vehicles, which places higher demands on the high efficiency and low noise of motors.
Disclaimer: This article is transferred from other platforms and does not represent the views and positions of this site. If there is any infringement or objection, please contact us to delete it. thank you! |