Dynamic inclination sensor with unique angle stability
Time:2022-11-23
Views:1487
Have you tried to hang a picture horizontally with a level? Yes, it‘s simple. When the drawing is hung horizontally, the bubble of the horizontal line will be displayed. Have you ever tried to keep the bucket level when accelerating, braking or driving on gravel roads or pits? No, of course not. In this case, neither the level nor the static inclination sensor can provide a meaningful value! The new IMU F99 tilt sensor launched by Pepperl+Fuchs provides a reliable tilt value for dynamic applications, because it can immediately filter out external interference (such as pits). The unique software adjustments made via the CAN bus also ensure excellent angle output, even when driving behaviour changes significantly.
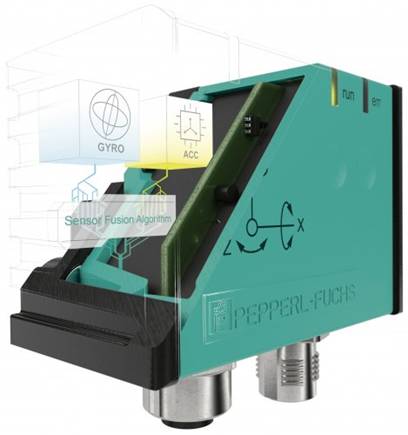
J1939 based IMU F99
When static tilt sensors are used for dynamically moving machines, such as wind turbines, AGVs, and machines for construction, agriculture, and forestry, they will soon reach their limits. This is because the angle change detected by the static tilt sensor is always on the same axis based on the gravity acceleration. Any additional acceleration trigger, such as braking or driving through a pothole, can cause significant interference that makes reliable angle measurement impossible.
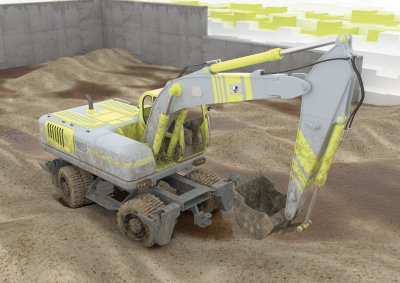
IMU F99 is used to determine the arm angle of the excavator
IMU F99 dynamic inclination sensor is specially developed for this dynamic application. Its core is to measure the speed and acceleration in all three spatial directions, and then combine them to generate angle values through intelligent algorithms. This makes it possible to obtain reliable angular output. It is clear, however, that different types of machine motion mean that rotational rates and accelerations need to be combined in a way that is appropriate for a particular machine. Therefore, Pepperl+Fuchs provides a unique and user-friendly adjustment setting, so that only one device can be used to perform position measurement in wheel loaders, bulldozers, cranes, etc.
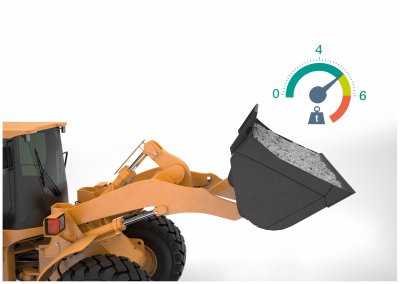
IMU F99 is used to determine the payload of wheel loaders
IMU F99 also provides rotation and acceleration of three axes in parallel with angle output. This means that the product can be used for a wide range of applications. For example, the device can be used to determine the speed of a wind turbine. At the same time, it can also monitor the blade acceleration, which may fluctuate when there is ice on the blade. This makes it possible to control the speed and perform predictive maintenance on the wind turbine.
Automation is our world. The perfect solution is our goal.
With the courage of entrepreneurship, fearless pioneering spirit and persistent innovation concept, Walter Pepperl and Ludwig Fuchs, the founders of Pepperl, jointly founded a radio repair factory in Mannheim in 1945. Many years later, they invented the world‘s first proximity switch, which confirmed their creativity. The close cooperation between Pepperl+Fuchs and its customers as well as its innovative automation technology and procedures have created the starting point of its glorious history. Today, we pay more attention to the personalized needs of each customer.
Whether as a pioneer in the field of electrical explosion-proof or an innovator in the field of efficient sensors, close cooperation with customers is the reason why we become the leader in the field of automation. Our goal is to combine our advanced technology with all-round services to optimize customer processes and applications.
Disclaimer: This article is transferred from other platforms and does not represent the views and positions of this site. If there is any infringement or objection, please contact us to delete it. thank you! |